Metal Injection Moulding Products
Review
Description
Metal injection molding (MIM) is a metalworking process in which finely-powdered metal is mixed with binder material to create a "feedstock" that is then shaped and solidified using injection molding. The molding process allows high volume, complex parts to be shaped in a single step. After molding, the part undergoes conditioning operations to remove the binder (debinding) and densify the powders. Finished products are small components used in many industries and applications.
Eyeglass components produced by powder injection molding
Complex geometry in one component instead of an assembly of many items
The behavior of MIM feedstock is governed by rheology, the study of sludges, suspensions, and other non-Newtonian fluids.
Due to current equipment limitations, products must be molded using quantities of 100 grams or less per "shot" into the mold. This shot can be distributed into multiple cavities, making MIM cost-effective for small, intricate, high-volume products, which would otherwise be expensive to produce. MIM feedstock can be composed of a plethora of metals, but most common are stainless steels, widely used in powder metallurgy. After the initial molding, the feedstock binder is removed, and the metal particles are diffusion bonded and densified to achieve the desired strength properties. The latter operation typically shrinks the product by 15% in each dimension.
The metal injection molding market has grown from $9 million USD in 1986, to $382 million USD in 2004 to more than $1.5 billion USD in 2015. A related technology is ceramic powder injection molding, leading to about $2 billion USD total sales. Most of the growth in recent years has been in Asia.
Material |
| Density 103kg/m³ | Hardness | Tensile Strength | Bending Strength Mpu | Extensibility |
Iron Base | MIM4600 | 7.68 | 85 HRB | 400 | / | 25 |
| MIM4650 | 7.68 | 100 HRB | 600 | / | 15 |
Stainless Steel | 316L | 7.94 | 52 HRB | 580 | / | 45 |
Tungsten Alloy | 95%W | 18.1 | HRC31 | 930 | / | 10 |
Hard Alloy | Yg8x | 14.9 | HRA90 | / | 2300 | / |
Characteristic | Precision Casting | MIM |
Minimum hole diameter | 2mm | 0.4mm |
2mm diameter of blind hole | 2mm | 20mm |
Minimum wall thickness | 2mm | < 1mm |
Maximum wall thickness | Unlimited | 10mm |
Tolerance of 4mm Diameter | ± 0.2mm | ±0.06mm |
Surface Roughness(Ra) | 5μm | 1μm |
Process
MIM gained recognition throughout the 1990s as improvements to subsequent conditioning processes resulted in an end product that performs similarly to or better than those made through competing processes. MIM technology improved cost efficiency through high volume production to "net-shape", negating costly, additional operations such as machining although MIM is weak in terms of tight dimensional specifications.
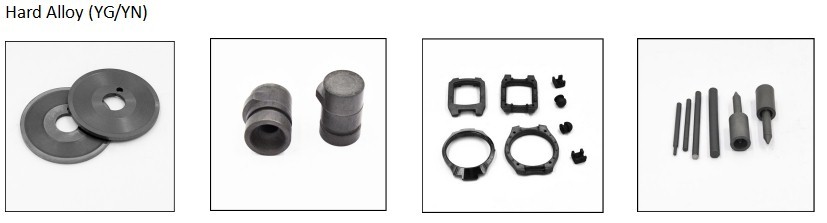
The window of economic advantage in metal injection molded parts lies in complexity and volume for small-size parts. MIM materials are comparable to metal formed by competing methods, and final products are used in a broad range of industrial, commercial, medical, dental, firearms, aerospace, and automotive applications. Dimensional tolerances of ±0.3% are common and machining is required for closer tolerances. MIM can produce parts where it is difficult, or even impossible, to efficiently manufacture an item through other means of fabrication. Ideally, at least 75 dimensional specifications in a component of just 25 mm maximum size and 10 g mass is best - as for example required for watch cases, cellular telephone plugs, and laptop computer hinges. Increased costs for traditional manufacturing methods inherent to part complexity, such as internal/external threads, miniaturization, or identity marking, typically do not increase the cost in a MIM operation due to the flexibility of injection molding.
There is a broad range of materials available when utilizing the MIM process. Traditional metalworking processes often involve a significant amount of material waste, which makes MIM a highly efficient option for the fabrication of complex components consisting of expensive/special alloys (cobalt-chrome, 17-4 PH stainless steel, titanium alloys and tungsten carbides). MIM is a viable option when extremely thin walls specifications (i.e., 100 micrometers) are required. Additionally, EMI shielding (Electromagnetic Interference) requirements has presented unique challenges, which are being successfully attained through the utilization of specialty alloys (ASTM A753 Type 4).