Carbon Fiber Rotor
- Share
- publisher
- Doris Yang
- Issue Time
- Aug 15,2023
Summary
High-speed permanent magnet motors offer advantages such as high-power density and efficiency. However, when using non-laminated steel for the rotor, there can be severe losses that may lead to irreversible demagnetization of the permanent magnets. Research has shown that replacing the high-conductivity non-laminated steel sleeve with low-conductivity carbon fiber composite materials can effectively reduce rotor losses.
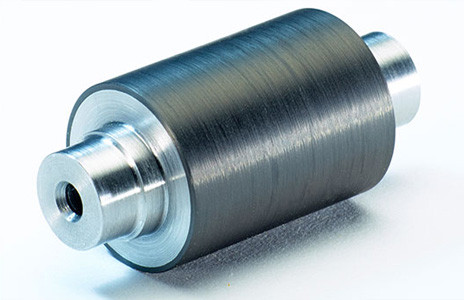
What
is Carbon Fiber?
Carbon
fiber is a fiber material with a carbon content of over 95%. It possesses
excellent mechanical, chemical, and electrical properties, making it known as
the "King of New Materials." It is a strategically important material
for both military and civilian applications, and due to its high price, it is
often referred to as "black gold. "Currently, most of the carbon
fiber used is produced from polyacrylonitrile (PAN) fiber.
The
process of converting PAN fiber into carbon fiber involves three main steps:
1.
Pre-oxidation of polyacrylonitrile at temperatures below 300℃, leading
to cerium molecular dehydrogenation, cyclization, and the formation of a
heat-resistant structure in preparation for carbonization.
2.
Carbonization in an inert gas at temperatures between 1000℃ and 1500℃, during
which the unstable components and non-carbon atoms in the structure are
removed, resulting in a disordered graphite-like structure with a carbon
content of over 92%.
3. To achieve even higher modulus fibers, a further graphitization process is performed at temperatures between 2000℃ and 3000℃ based on the carbonized fibers.
Note:
The process description may involve some technical terms and may not be an
exhaustive account of all carbon fiber production methods.
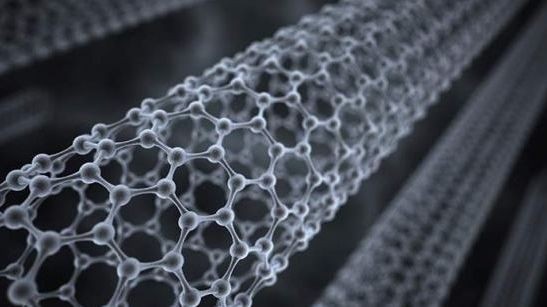
Why
fiber sleeve becomes more and more popular? Here are some reasons:
1.
High forming efficiency & Small forming damage
The
preparation method with high efficiency and low damage has difficulty realizing
the application of sleeve engineering. The two-step prestressing manufacturing
method of winding first and then press-fitting has the disadvantages of a
complicated preparation process and easy damage to the rotor. The one-step
prestressing manufacturing technology of large tension winding with low damage
and high preloading effect has obvious advantages.
2.
Easy realization of stress design
In
recent years, researchers have adopted the high-tension winding method to
prepare the carbon fiber sleeve for the rotor of a permanent magnet motor, and
the one-step method is used to form the sleeve pre-tightening, which provides
pre-tightening force for the permanent magnet while preparing the carbon fiber
sleeve and can make the stress distribution of the sleeve uniform by designing
the tension of the winding layer.
3.
High preloading effect
High-speed
permanent magnet motors offer advantages such as high-power density and
efficiency. However, when using non-laminated steel for the rotor, there can be
severe losses that may lead to irreversible demagnetization of the permanent
magnets. Research has shown that replacing the high-conductivity non-laminated
steel sleeve with low-conductivity carbon fiber composite materials can
effectively reduce rotor losses.
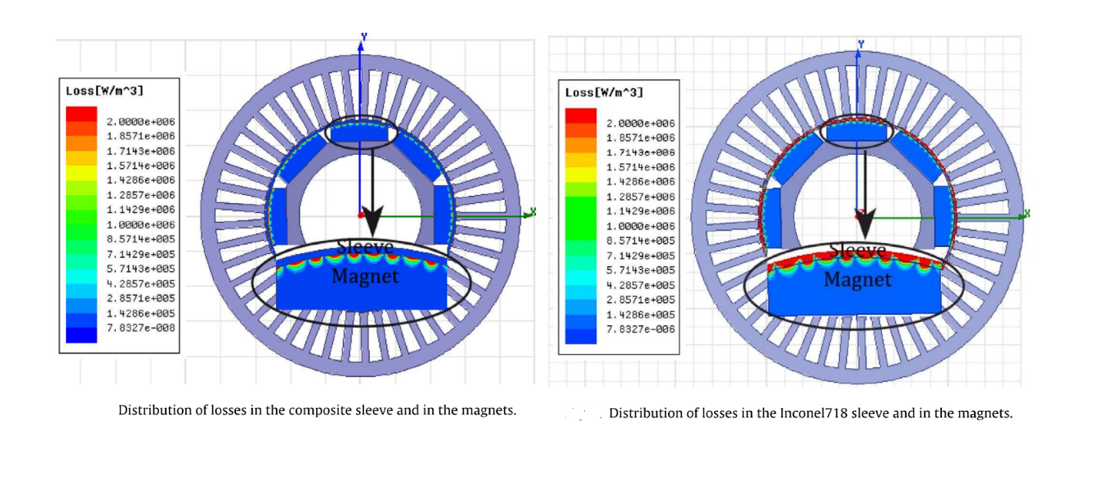
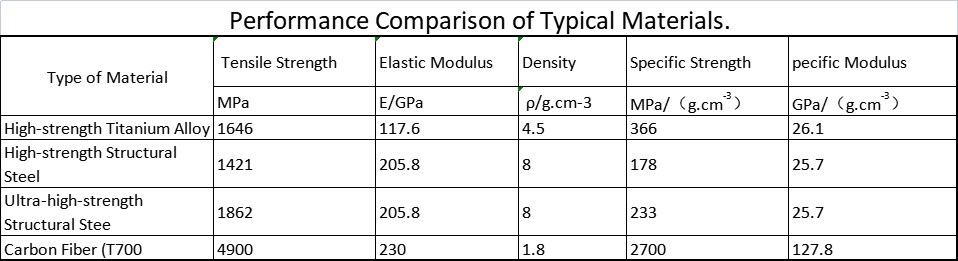
The
conventional manufacturing methods for carbon fiber rotors include the
press-fitting method and the tension-tension winding method.
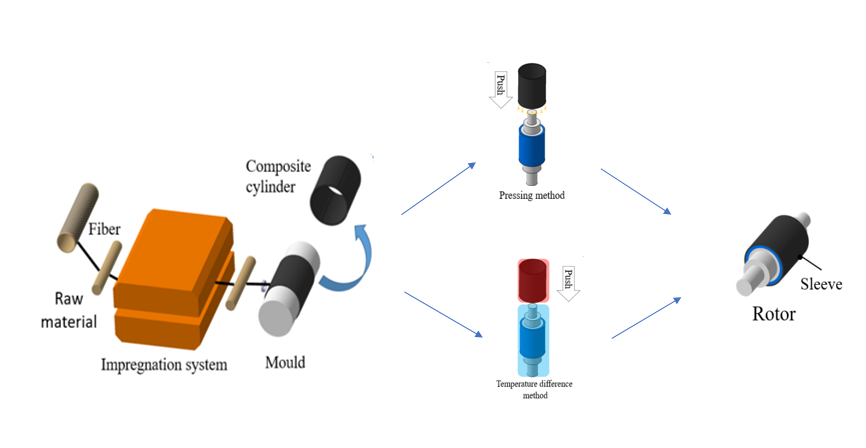
In engineering
applications, the assembly methods for interference fit components mainly
include press-fitting, cold assembly, and hot-fit methods.
The
process flowchart for manufacturing the rotor using the press-fitting method is
as left picture: first, wind the fiber bundles layer by layer on the surface of
the mold that ensures the inner diameter accuracy of the sleeve. When the
winding layer reaches a certain thickness, cure it and then demold to obtain
the carbon fiber sleeve. Subsequently, the permanent magnet is pressed into the
sleeve using a hydraulic press.
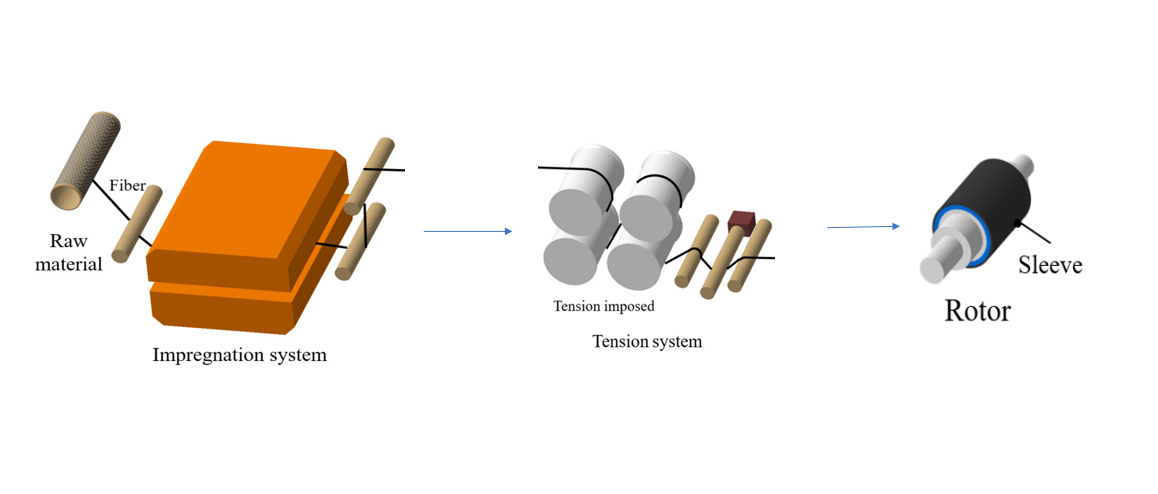
2. Tension-tension winding method
The
tension-tension winding method for manufacturing the rotor does not require a
mold. Instead, the fiber is directly wound around the surface of the permanent
magnet. During the winding process, a sufficient initial tension is applied to
the fiber bundle. This results in the carbon fiber sleeve already having a
certain pre-compressive stress on the permanent magnet after curing, thereby
protecting the safety of the permanent magnet.