What is NdFeB hydrogenation crushing HD method
- Share
- Issue Time
- Aug 29,2022
Summary
NdFeB hydrolysis (HD) method is to refine the particle size by hydrogen absorption lattice expansion and dehydrogenation reduction, and hydrogen absorption or dehydrogenation is a reversible chemical reaction process, and the physical and chemical reactions have changes in its chemical composition and magnetic properties.
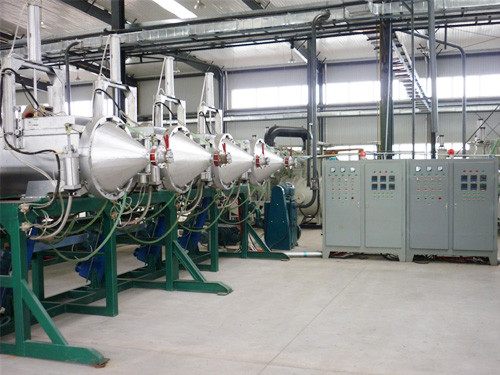
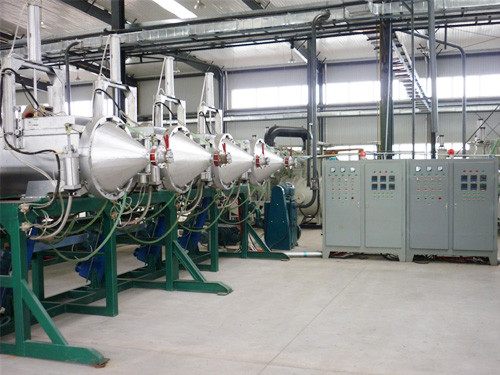
The
NdFeB hydrogenation pulverization HD method is only suitable for the coarse
crushing and middle grinding of hydrogenated metals or alloys. The feed size is
100-0.1MM, and the powder size is 10-1000UM. Need powder, this particle size
has met practical requirements. The powder particle size of NdFeB permanent
magnets should be 3-5UM, and it needs to be finely ground by jet mill. The
NdFeB hydrolysis (HD) method is to refine the particle size by hydrogen
absorption lattice expansion and dehydrogenation reduction, and hydrogen
absorption or dehydrogenation is a reversible chemical reaction process, and
the physical and chemical reactions have changes in its chemical composition
and magnetic properties. NdFeB absorbs hydrogen, the resulting hydride lattice expands,
and generates heat, a chemical process; the internal stress of the expansion
makes the NdFeB crystal crack into a loose body, which is a physical
phenomenon, both of which are carried out at the same time; heating
dehydrogenation treatment, most of the main The phase hydride changes back to
the original Nd2Fe14B powder, and some residual Nd-rich phase hydride needs
advanced treatment. In the hydrogen absorption process of NdFeB, the first
hydrogen absorption is the Nd-rich phase exposed on the surface, followed by
the reaction of the main phase Nd2Fe14B with H2, the formation of the main
phase hydride is accompanied by an exothermic reaction, and the total heat can
make the reactant temperature Raised to 300 degrees. The lattice constant
becomes larger and the thermal expansion process produces powder explosion, and
the HD powder of NdFeB has undergone qualitative change. Dehydrogenation turns
Nd2Fe14Bhy into Nd2Fe14B, i.e. decomposition of the hydride. Effects of
temperature and pressure, 650℃, the Nd-rich phase changes and melts, and
the HDDE reaction occurs when the temperature continues to rise. The optimal
dehydrogenation temperature is 500 ℃, Under this condition, all the
hydrogen of the main phase hydride is released, and the NdH3 of the
neodymium-rich phase hydride is 500. After C, part of the hydrogen is removed
to become NdH2, 1040.℃ can completely discharge hydrogen from the main phase
Nd2Fe14B.
①The
milling efficiency of HD+JM (jet mill) is increased by 2-3 times, reaching
90-100KG/HR (original only 30KG/HR); it is close to the main phase composition
of NDFEB (RE=11.76at%) in terms of mechanical properties, and Hard and tough
(Hv=530, flexural strength 24-26KG/mm2);
②Effectively reduce the oxygen content of NdFeB alloy magnetic powder.
The HD hydrogenation pulverization method effectively reduces the oxidation
degree of the grinding section ((200-800)×10-O2), and the presence of hydrogen
in the sintering process can reduce the amount of neodymium Oxide, purifies
grain boundaries and promotes densification, realizing partial activation
sintering.
③HD powder is mostly cracked along the grain boundary phase: HD+JM
powder is mostly single crystal particles, close to the optimal particle size
of 2-3UM, and the edges of the grains have neodymium-rich phases, which can
effectively improve IHC, which can actually increase by 500-5000Oe.
④ The properties of HD NdFeB alloy magnetic powder vary slightly:
HD+JM powder exists in the form of oxide due to part of the powder, its
magnetic variation presents: 4πJs high, Br and IHC low phenomenon, weak
magnetic, easy demolding, neat appearance, stacking convenient;