Current Development and Application of domestic axial flux motors
- Share
- publisher
- Gordon
- Issue Time
- Jan 12,2022
Summary
Axial flux permanent magnet machine (AFPMM), also known as disc permanent magnet motor, has attracted more and more attention due to its compact structure, high efficiency, and high-power density. AFPMM is especially suitable for applications that require high torque density and compact space, such as electric vehicles, renewable energy systems, wheel-eating energy storage systems and industrial equipment.
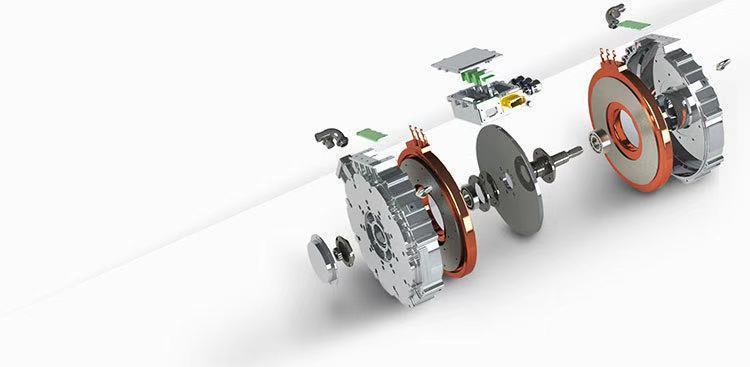
The current development and application of domestic axial flux
motors
The axial flux permanent magnet synchronous motor has an axial
flux direction, which determines its structure is different from the ordinary
radial motor. Under the same external dimensions, the core advantage of the
axial flux motor lies in the rotor with a larger diameter, it rotates along the
stator rather than inside it. Torque equals force times radius, and an axial
flux motor can get more torque for the same force. This means that the axial
flux motor can output more torque for the same volume of permanent magnets and
copper winding material.
Axial flux motors offer a 30% torque density advantage over
conventional radial motors.
Axial flux motors have many advantages, such as small size, low
noise, high power density, and excellent heat dissipation performance.
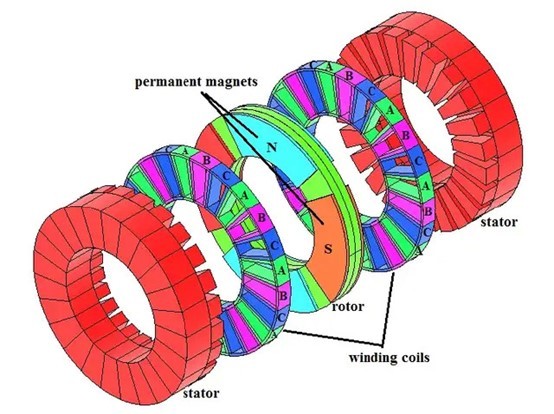
It can be seen from the structure diagram that, different from
the radial flux motor, the stator and rotor of the axial flux motor attract
each other and generate an axial force. We all know that the metal is not
resistant to compression, and the axial force is the most feared by the motor.
Lightly, it will increase friction and aggravate vibration. Therefore, the
axial flux motor generally adopts the design of double stators on both sides
and a single rotor in the middle. There are also schemes such as single stator
double rotor and multi-disk type to offset the axial force. Secondly, the gap
between the stator and the rotor is called the air gap, which is an
indispensable part of the magnetic circuit of the motor. The axial flux rotor
is laid flat on top of the stator, and the air gap area is significantly
larger. Its surface flatness and gap uniformity are extremely demanding.
This means that the requirements for machining and manufacturing
accuracy and assembly accuracy are very high, which brings extremely high
manufacturing costs and extremely low production flexibility.
The high manufacturing difficulty also leads to the insufficient
production scale of the axial flux motor, the small market capacity, and the
inability to keep up with the matching parts. Not only the axial flux motor
itself, but also after connecting the drive shaft, the axial movement generated
by the rear end load will also seriously affect the magnetic balance between
the rotor and the stator of the axial flux motor. Once the critical point is
exceeded, the rotor will be adsorbed to the stator. up, it would be a disaster.
These drawbacks in turn lead to difficulties in the application
of axial flux motors, resulting in fewer practitioners in this field, low
product maturity, and lack of R&D verification systems. Under the cycle, it
is difficult to compete with ordinary radial flux motors.
At present, what is the development of the disc motor in China?
What special scenarios are disc motors suitable for?
At present, the mainstream motors in automobiles and
construction machinery in China are still mainly permanent magnet radial
motors, which mainly rely on its high speed and through the high gear ratio
gearbox to achieve the process of reducing speed and increasing torque. Most of
them have a long cylindrical shape with a small diameter and a large axial
dimension. The axial flux motor is just the opposite. Because of its
disc-shaped structure, the magnetic field action area is enlarged, which makes
the power generation efficiency higher. Most of them have the characteristics
of large diameter and thin axial size.
From the current point of view, the development of axial flux
motors in China has shown a multi-point blooming situation. There are many
enterprises engaged in the development of axial flux motors in Jiangsu,
Zhejiang, Shanghai and Beijing. Compared with the private customization of YASA
and Magnax in foreign countries, most domestic enterprises aim at mass
production, optimize the material and structure of the motor, and sacrifice a
certain power density to achieve a motor that meets market demand and is
reasonably priced. level.
From the perspective of the application scenarios of disc
motors, it can be subdivided into the field of elevators, commercial vehicles
and buses, construction machinery, generator sets, range extenders, military
and aerospace fields, etc.
1. Elevator field. KONE Elevator, with its own developed disc motor traction machine (also a disc motor), once stood on the commanding heights of the elevator industry. Relying on its flattening advantage, the traction machine is placed between the elevator car and the shaft wall, eliminating the traditional traction machine room, also called a machine room-less elevator.

2. Commercial vehicles and buses. The P2 motor of the commercial
vehicle (the motor is placed between the engine and the gearbox) can perform
power transmission during rapid acceleration and energy recovery during
braking. This directly reduces fuel consumption and is also in line with the
implementation of current environmental protection policies. The use of the
disc motor effectively solves the problem of excessive axial size of the engine
+ motor + gearbox, which plays a good role in the layout of the interior space.
Similarly, the wheel-side motor of the pure electric bus is also a model with a
low floor and a wide aisle due to the thin axial size of the disc motor.
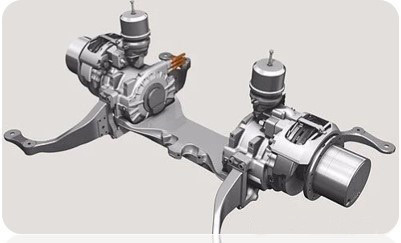
3. Construction machinery and off-road vehicles. In loaders,
forklifts, industrial ceiling fans, mining trucks, sweepers, etc., it is mostly
used in lifting motors, travel motors, fan motors, and main drive motors. With
its thin thickness, high power density and low rotational speed, customers'
solutions can be optimized.
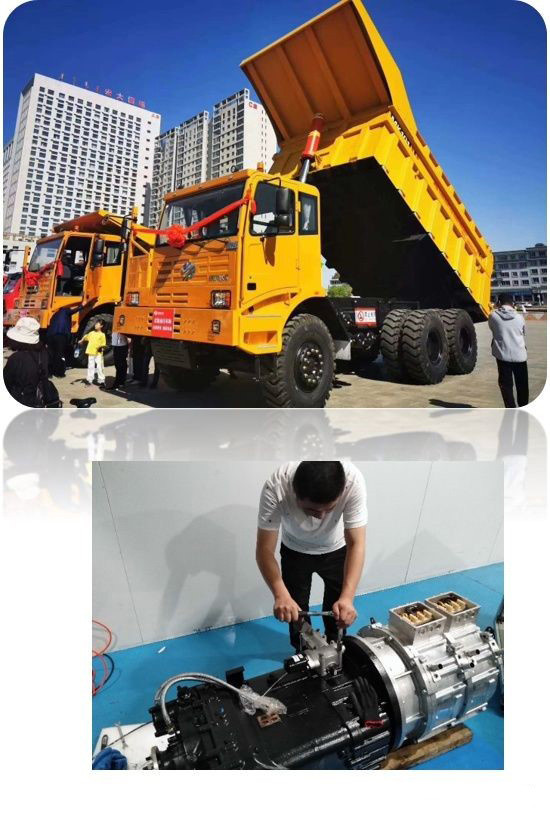
4. Range extender, generator set field. At present, the program
extension market is very hot, which is also related to its high cruising range
and low fuel consumption. Many related passenger cars and commercial vehicles,
as well as unmanned field vehicles, have developed extended-range products. The
comprehensive fuel consumption will save about 30% of fuel consumption compared
with fuel vehicles. In the field of generator sets, the disc motor can be said to
subvert the traditional generator set. The air-cooled asynchronous machine is
replaced by a disc permanent magnet motor, which greatly reduces the size and
weight of the generator set, and also greatly improves the power generation
efficiency. Widely used in generator sets between 1-100kw.
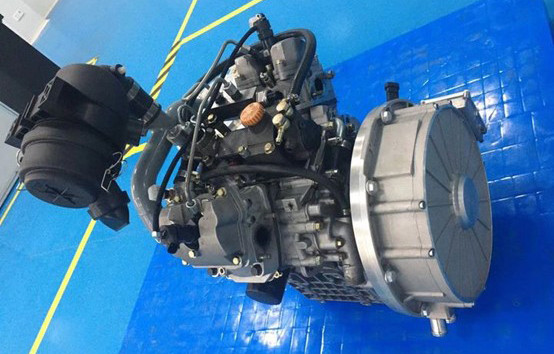
5. Military and aerospace products. Relying on the high-power
density of the disc motor, it has been well used in pure electric aircraft, and
can even achieve a natural air-cooled structure! In the field of military
industry, it is more used in battlefield in-wheel vehicles. The in-wheel motor
makes the vehicle more comfortable with its excellent steering ability and
narrow space layout.