How To Optimize Magnet Cost?
- Share
- publisher
- Evan
- Issue Time
- Sep 24,2021
Summary
The reduction in cost means the enlargement of profit margins, and it will have stronger competitiveness in the market. Here we discuss how to reduce costs healthily and effectively from the aspects of management improvement, process optimization, technological innovation, and manufacturing innovation.
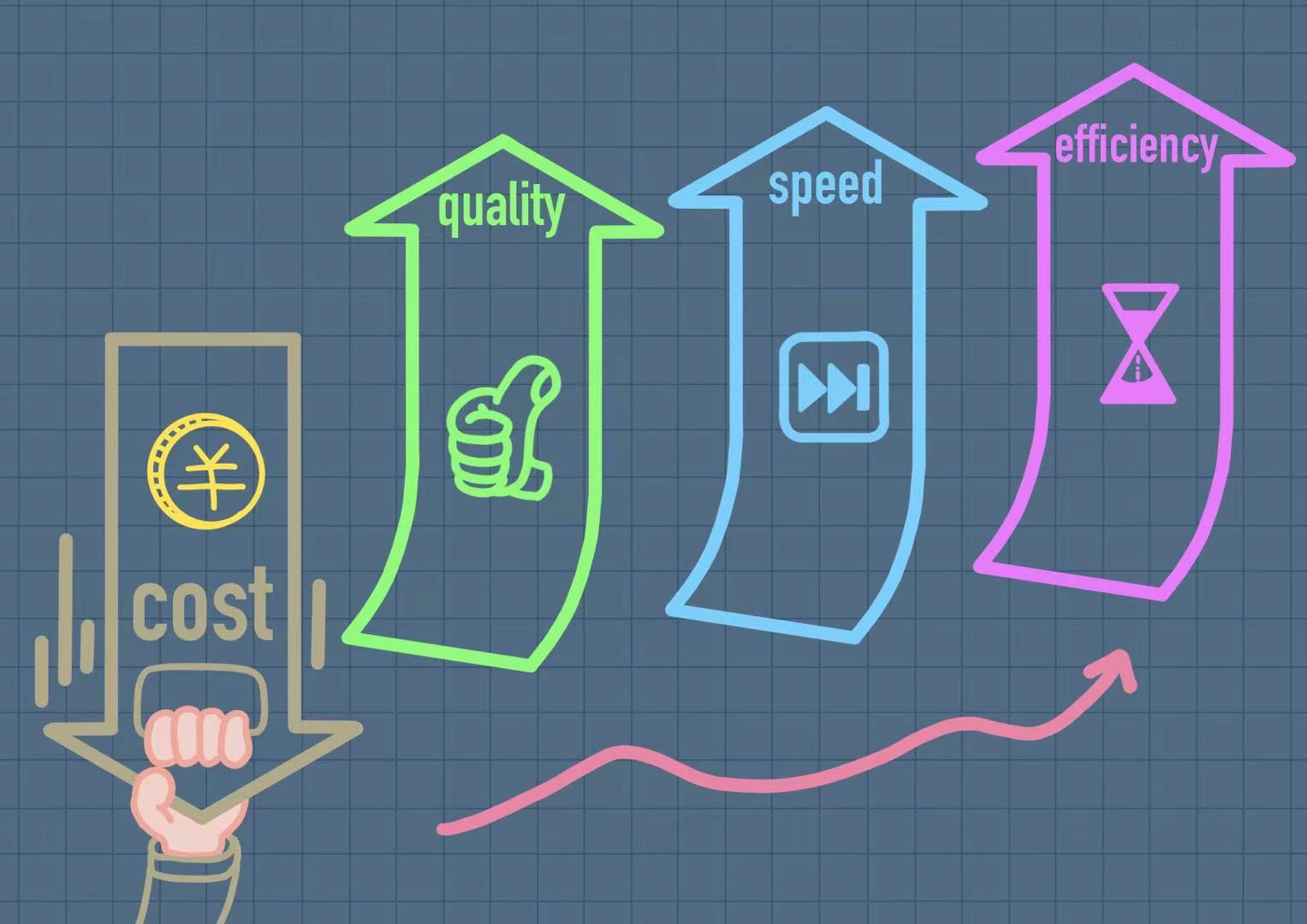
An enterprise is
a profit-oriented organization, and it is facing unprecedented operating
pressures currently. These pressures come from the demands of business growth,
accelerated innovation, and continuous improvement in productivity, as well as
market competition, globalization trends, the pace of information technology
and business change is accelerating, also from the need to reduce costs.
The reduction in
cost means the enlargement of profit margins, and it will have stronger
competitiveness in the market. Here we discuss how to reduce costs healthily
and effectively from the aspects of management improvement, process
optimization, technological innovation, and manufacturing innovation.
Most of
manufacturing enterprises have relatively rapid initial development, rapid
business expansion, and rapid expansion of production capacity, but actual
profits are gradually shrinking, mainly due to the lack of effective management.
Although most of them have applied for quality certificates, ISO9001, etc. the
actual operation of the system is not effective, eventually turned into a piece
of paper. The effective implementation of the quality system is conducive to
controlling and reducing costs, helping companies seek ways to improve product
quality. The management can also grasp the problems in quality management, and
at the same time can broaden the cost management channels. In addition to the
effective operation of the system, the use of quality tools, such as SPC, MSA,
FMEA, APQP, PPAP, etc. can help companies in the manufacturing process to help
us find the variation in the process, and take corresponding measures to
restore production to normal, to reduce the defects caused by mutation, thereby
reducing the cost of poor quality
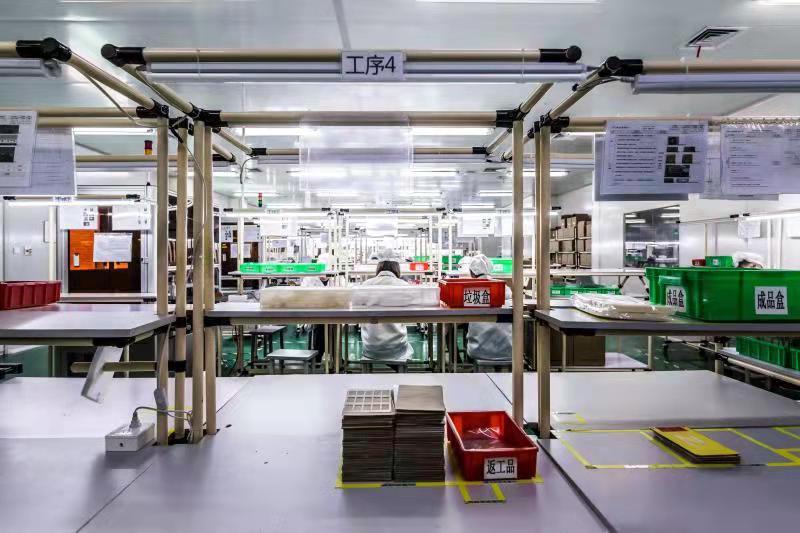
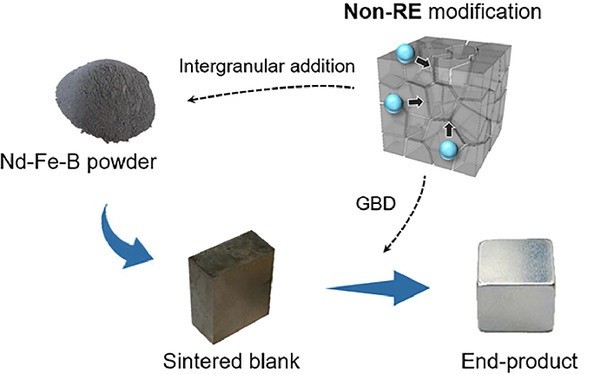
Technological
innovation is of great significance to the production process of products. It
can not only greatly improve the production efficiency of enterprises, but also
bring about cost reduction and win opportunities in market competition. For
example, the current permanent magnet motors used in new energy vehicles need
to use high temperature resistant neodymium iron boron magnets. During the
manufacturing process of such magnets, a certain proportion of heavy rare earth
element Dy needs to be added to the formula, which greatly increases the cost
of the magnet. With the manufacturing innovation of the magnet technology, the
grain boundary diffusion technology not only meets the performance requirements
of the magnet, but also greatly reduces the amount of heavy rare earth used,
resulting in a substantial cost reduction.
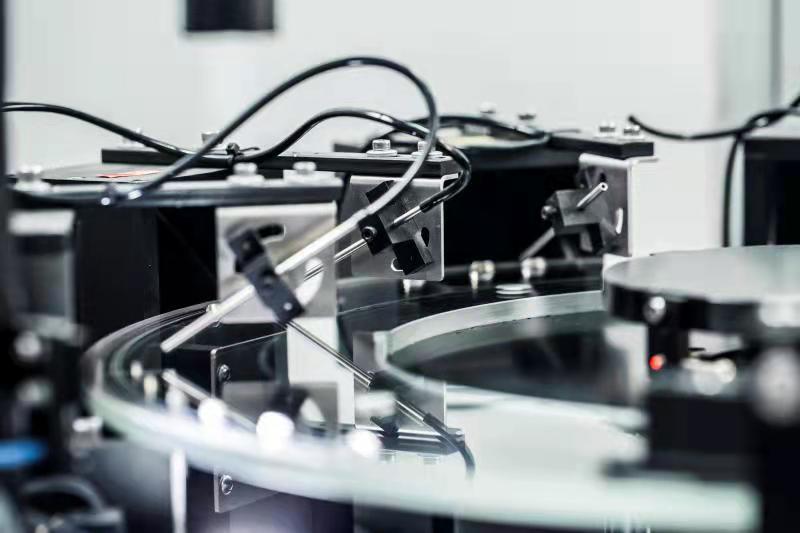
Nowadays, the
highest cost is labor cost. In the six major factors that affect quality,
human, machine, material, method, environment, and measurement, the process
variation is caused by human factors, and the probability of causing defects is
the highest. In the manufacturing inspection process, people often make
mistakes due to fatigue, and the efficiency of labor is also a major factor
that restricts productivity. Automation equipment is a good solution. The
introduction and use of automation equipment can greatly improve production
efficiency. For example, in the magnet manufacturing process, one automation
equipment can complete the four processes of
identification-magnetization-inspection-packaging together. The efficiency is
many times that of manual work, and it is not easy to make mistakes.