How to weld magnetic weldments?
- Share
- publisher
- Evan
- Issue Time
- Jan 20,2021
Summary
In the production of oilfield construction, the welding of magnetized tube is often encountered. Due to the large magnetic bias when welding the magnetized tube, the weldability is poor.
This article mainly introduces the use of demagnetization shielded metal arc welding of direct current (DC), alternating current (AC), electromagnet or permanent magnet for welding magnetized tube.
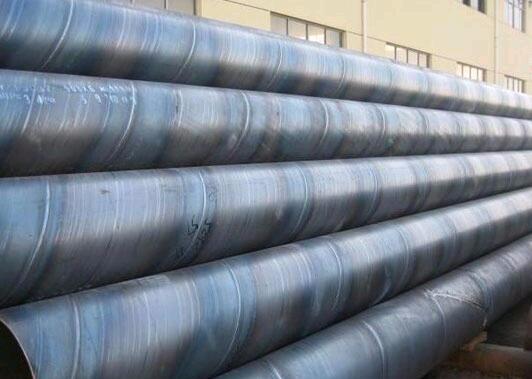
In the production of oilfield construction, the welding of magnetized tube is often encountered. Due to the large magnetic bias when welding
the magnetized tube, the weldability is poor.
This article mainly introduces the use of demagnetizing shielded metal arc welding of direct current (DC), alternating current (AC),
electromagnet or permanent magnet for welding magnetized tube.
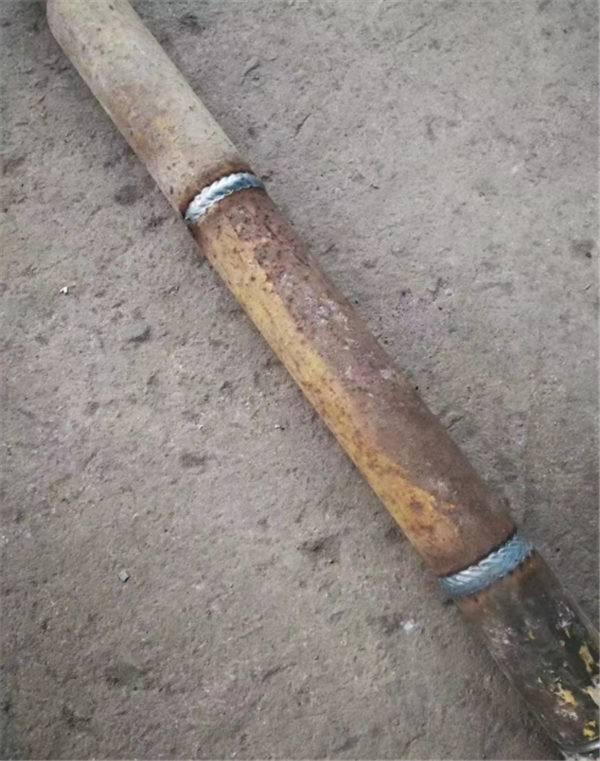
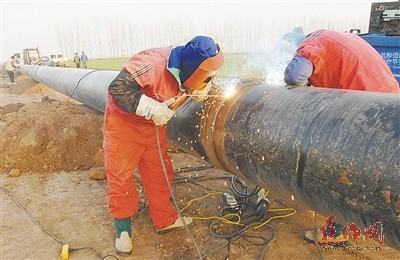
Causes of remanence and its influence on welding quality
In the oilfield production, when welding heat pipelines and gas injection pipelines, magnetic blows sometimes occur and affect the entire welding process. The formation of magnetic blows is the result of remanence in the tube metal.
Generally, remanence is divided into induced magnetism and process magnetism.
Induced magnetism is often generated in the pipe-making process of the factory, such as when electromagnetic cranes are used for loading and unloading, steel pipes are parked in a strong magnetic field, non-destructive inspections are completed by magnetization, and steel pipes are placed close to strong power supply lines.
Process magnetism often occurs during assembly welding operations, and also occurs during the use of magnetic gripper, fixture, DC welding pipe. Long-term contact with electrical wires connected to a DC power source will also generate process magnetism.
There are various difficulties when welding magnetic steel tubes, such as the arc combustion stability is poor, the arc deviates from the electrode axis, the liquid metal and the slag splash from the welding pool, and the welding pool cannot be established in severe cases, which cannot make the welding. In order to stabilize the welding process and improve the quality of welded joints, the magnetized steel pipe must be demagnetized before welding. It should be pointed out that it is difficult for the welded steel tubes to achieve complete demagnetization. When the remanence is insufficient to affect the welding quality, welding is allowed.
Demagnetizing method
Most of the oilfield construction is carried out in the field. When the tubes are welded and prefabricated, the corresponding tubes demagnetization process measures are specially formulated.
Analysis of remanence parameters and combined with the specific conditions of the construction site to choose the demagnetization method:
Electromagnetic coil composed of welding wires with a cross-section of 35-50mm² is used to complete the demagnetization of direct current and alternating current. The wire is wound on a steel tube or two butt-connected steel tubes, and is wound into coils with different turns according to the remanence of the steel tubes.
When degaussing with DC, an arc welding rectifier with a current of 300~700A must be used.
When degaussing with AC, an arc welding transformer with a current of 300-700A must be used.
With the help of a dedicated electromagnet for demagnetization, an arc welding rectifier or an arc welding transformer should be used as a power source.
When degaussing, the magnetic field should be greater than the remanent magnetic field. HI=(1.2~1.5)H2, where H1 means degaussing magnetic field strength and H2 means remanent magnetic field strength. The degaussing magnetic field strength is determined by the formula: H=I•N/L, where I is coil energizing current, N is degaussing coil turns number, L is winding length.
In order to measure magnetism, it is recommended to use the HMⅡ-97X magnetometer. The magnetometer is a portable instrument used to evaluate the magnetic induction intensity of the pulsating magnetic field and the leakage magnetic field in the air gap of the magnetic system. The magnetometer consists of a measuring converter, electronic device and charging device composition, the power supply of the instrument is a 9V battery built-in battery pack.
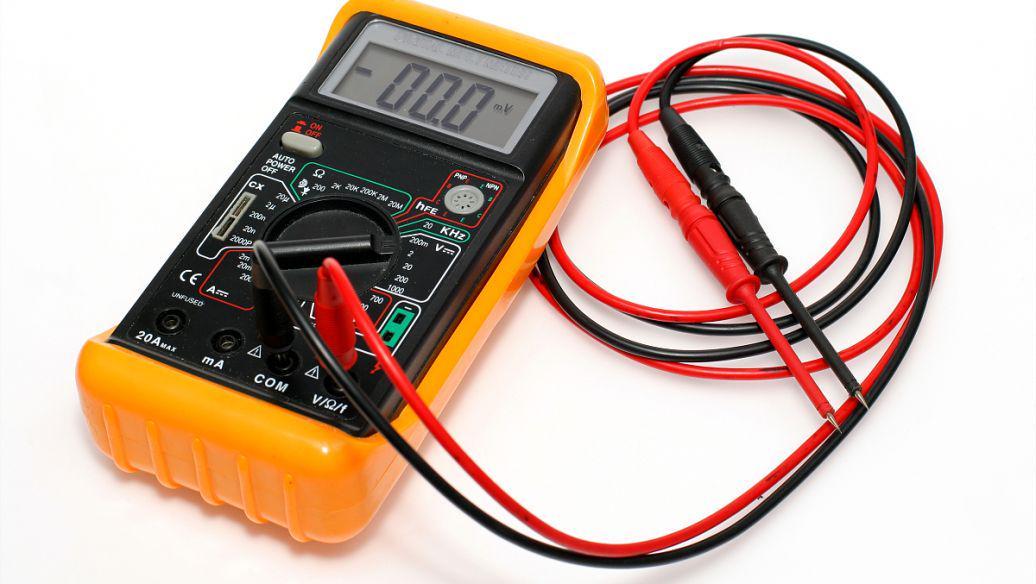
As mentioned earlier, there are three methods of demagnetization:
1.Direct current (DC) demagnetizing shielded metal arc welding.
2. Alternating current (AC) demagnetizing shielded metal arc welding
3. Electromagnet or permanent magnet demagnetizing shielded metal arc welding.
1. Demagnetizing with direct current
a. Determine the magnitude and direction of the remanence magnetic field of the steel tubes with the help of a magnetometer;
b. Arrange a coil composed of a flexible welding wire with a cross-section of 35-50mm² on the steel tubes, and connect it to the arc welding rectifier to make the magnetic field formed in the opposite direction to the remanence magnetic field of the steel tubes.
c. At the beginning of demagnetization, the current is 80 -100A.
d. During the demagnetizing process, the results of the demagnetizing magnetic field must be checked periodically on the steel tube with a magnetometer (measured when the power is turned on), and if necessary, controlling the current or changing its direction will be needed.
e. After the demagnetization, in order to reduce the magnetic flux smoothly, the current should be gradually reduced within 1 minute to zero, and then the power supply should be cut off.
Single steel tube demagnetization: A coil of 8.12 turns is wound around the outer circle at one end of the steel tube and demagnetized with the largest magnetic field, then the other end of the steel tube is demagnetized in the same way. When a single steel tube is demagnetized to the butt joint of the steel tube, the distance between the two steel tubes is not less than 300mm, and a coil of 18-20 turns is wound at a distance of 80-100mm from each tube end to complete the demagnetization.
When the butt joints of the steel tubes are demagnetized, a welding wire with a cross-section of 35-50mm² is wound around the ends of the butt-joined steel tubes to form a common coil of two steel tubes. The coils can be overlapped (clockwise or counterclockwise), and the total number of turns is 16-22. At this time, the larger number of turns should be on the steel tube with larger remanence. When the measured remanence level is less than 20×10-4T, the welding of the root of the weld is completed, which is the best demagnetization process.
Under special circumstances, short-circuit the welding tongs with the welding rod to the other end of the electrode for 10 seconds at a current of 300A, and then disconnect it. After each short-circuit and one disconnection cycle, check the magnetism with a magnetometer. Repeat the demagnetizing process if necessary.
2. Demagnetizing with alternating current
Mainly used at the end of a single steel tube and the end of butt-joined steel tubes with a wall thickness of 25mm. At this time, in addition to the demagnetization according to the above method, there is other method. A coil composed of a welding wire is used to connect a steel wire with a length of 0.5 to 1.0m and a diameter of 1.5 to 3.0m in the loop. The wire sits on a backing plate of an insulating and non-combustible material, such as asbestos brick. The steel wire can smoothly change the magnitude of the energized current, thereby changing the magnitude of the demagnetizing magnetic field. When the power is turned on, the steel wire is heated and burned out within a certain period of time. The burning time depends on the wire diameter, length and current value. After the steel wire is burnout, check the remanence with a magnetometer. When the demagnetization effect is insufficient, the demagnetization process must be repeated. The demagnetizing system can be removed after welding the root weld, and it is recommended to remove it immediately after demagnetizing.
3. Demagnetizing with electromagnet and permanent magnet
The electromagnet demagnetizing is mainly used on the steel tubes that have been butted, and the individual sections with a length of 100-200mm, especially near the magnetic field whose sign changes. At this time, after the demagnetization of individual sections, the welding of the root weld should be completed, and then the demagnetization of the next section. In order to demagnetize, an electromagnet with a special structure is selected. The electromagnet is installed at the butt joint of the steel tube so that the N pole of the electromagnet is placed on the edge of the steel tubes with the magnetic S pole, and the S pole of the magnet is connected with the magnetic N pole of the tube. In the demagnetization process, the direction and magnitude of the remanent magnetism of the steel tubes must be measured regularly with the help of a magnetometer (when the power is turned on). The magnitude of the demagnetizing magnetic field is adjusted by changing the size of the current, and the direction of the magnetic field is adjusted by changing the direction of the current, which means switching the positive and negative electrodes of the power supply to adjust.
C-shaped or cylindrical permanent magnets are used to demagnetize. When the magnet is installed correctly, the magnetic pole should be opposite to that of the magnetized butt steel tube. The correct installation of the magnet can be checked with a magnetometer. In order to enhance the demagnetization effect, the magnets can be connected to each other (two or three or more), which has the same effect. After the butt joint section is demagnetized, the welding of the root weld must be completed here. In order to increase the demagnetizing magnetic field, the magnet should be close to the demagnetizing place, otherwise the magnet can be removed. When the magnet is moved along the surface of the steel tube, the remanence at the butt joint of the steel tube can be reduced to a minimum.
In order to change the direction of demagnetizing magnetic flux, the c-shaped magnet must be rotated to 180° on the horizontal plane, and the cylindrical magnet installed on the edge of the butt joint must be exchanged or rotated by 180° in the vertical plane. After each demagnetization process, a magnetometer must be used to check the size of the remanence.
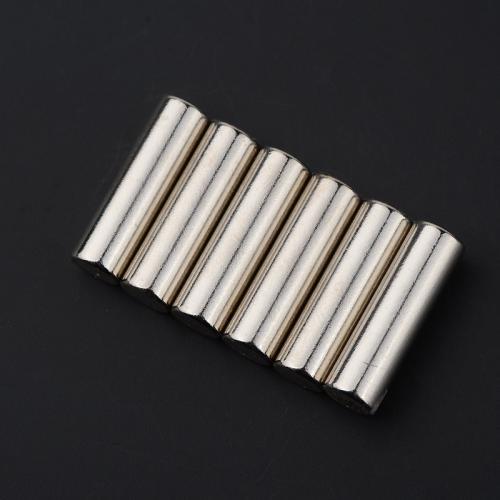
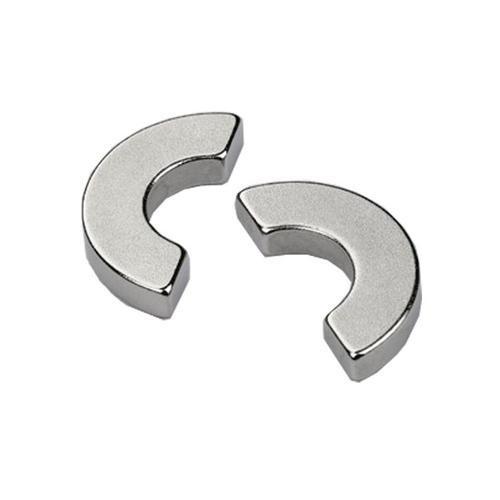
Conclusion
To sum up, in production, the construction conditions, welding process and production efficiency should be considered comprehensively to achieve high-quality welds safely, efficiently and at low cost under good working conditions. The basic principles for the selection of welding methods for magnetized tubes :
Due to the low flame temperature, small heat input and wide heat-affected zone, the traditional local flame heating demagnetizing electrode arc welding leads to the burning loss of alloy elements and the decrease of mechanical properties of base metal.
The overall heating and demagnetizing welding method is not easy to realize due to various factors of actual construction conditions.
It is recommended to use permanent magnets for demagnetization in places where the steel pipe butt joints have low magnetism and poor construction conditions.
It is recommended to use direct current for demagnetization in places where the magnetism is strong in the butt joint of the steel tube.