Mechanical processing
- Share
- Issue Time
- Dec 30,2020
Summary
Machining is a process that uses processing machinery to change the dimensions
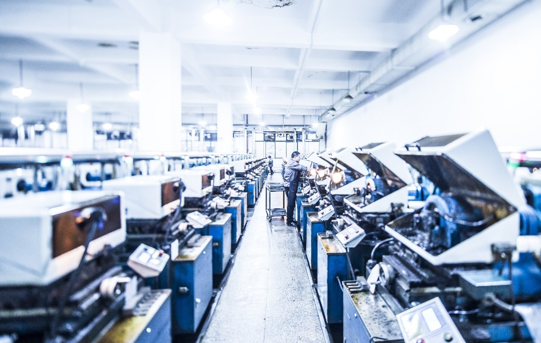
Machining is a process that uses processing machinery to change the dimensions or performance of the workpiece. According to the temperature state of the workpiece that to be processed, it is divided into cold processing and hot processing. Generally processing at room temperature, and does not cause chemical or phase changes of the workpiece, called cold processing. And processing at higher or lower than normal temperature that will cause chemical or phase changes of the workpiece called thermal processing.
Machining methods can be divided into two types. One type is a blank manufactured by hot working methods such as casting, forging or welding, and the size and shape of this kind of blank are inaccurate, and the surface is rough. To change the state of this blank, part of the surface metal must be cut off to meet the exact requirements of size and shape. This kind of machining to cut off the surface layer of the blank is called cutting. The other type is to apply pressure on the surface of the workpiece to change its size and shape to produce a part that meets the quality requirements. This is pressure processing in which the size and shape of the metal are changed by plastic deformation without cutting off the surface layer of metal, also called non-cutting processing.
Vector magnet production mainly uses cold machining and cutting, there are six mainly magnetic processing methods were used:
1.Double-Side Surface Grinding
The double-side surface grinding machine is a high-efficiency surface processing machine tool. It grinds two parallel end faces at the same time in one processing process. According to the layout, it can be divided into two types, horizontal and vertical. According to the feeding method, it can be divided into three types, through-type, Turntable type, come and go type. Because the ground products have high precision and high production efficiency, they are widely used in many industries, such as automobile, motorcycle, bearing, and magnetic materials.
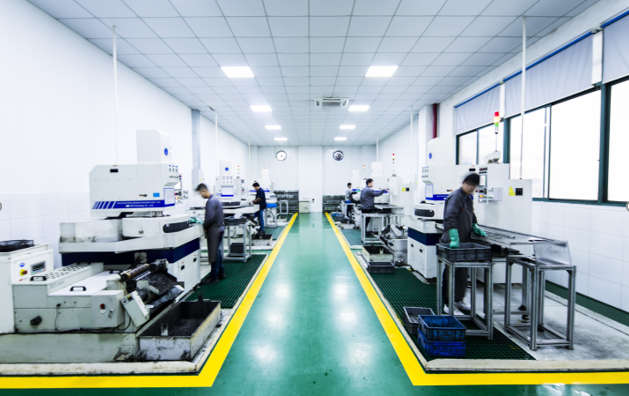
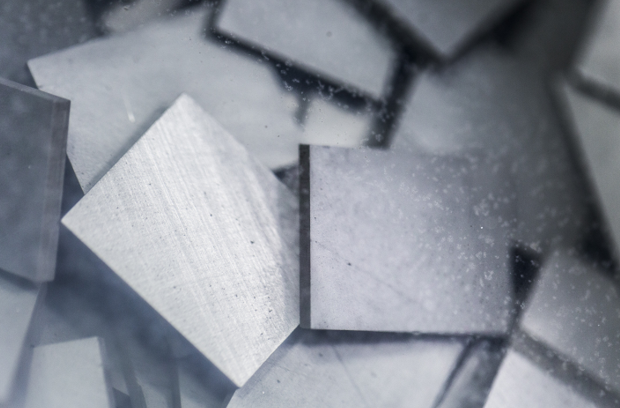
Centerless grinding is a kind of grinding process. There are two grinding wheels, a guide wheel and a grinding wheel. The guide wheel drives the cylindrical workpiece to rotate on the shim, and the grinding wheel has a grinding effect on the workpiece. In grinding, the choice of grinding wheel particle size is also very important. Coarsness centerless grinding wheels are often used for rough grinding and can only process workpieces that are not demanding. This method will be used for large number processing and in order to speed up the grinding speed. Also, this method will be used for the first processing of the workpiece, which is due to its relatively fast processing speed, but the degree of finish of the workpiece is low. To the contrary, the process speed of fine-grained centerless grinding wheel is slightly slower, but the processed workpiece has a high finish. If the particle size is selected appropriately, the mirror effect can be achieved. Therefore, the choice of centerless grinding wheel is based on the workpiece technical process requires specific selection.
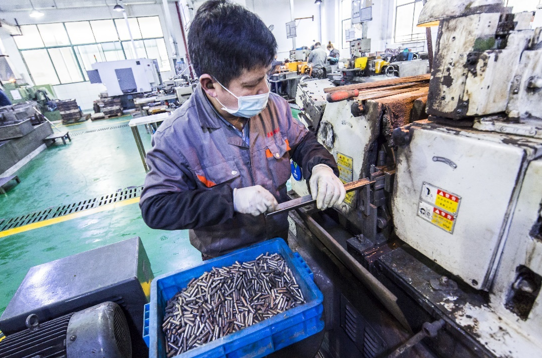
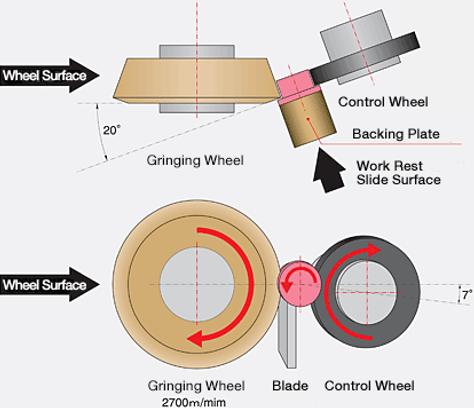
The working principle of the slicer is relatively simple, which is to use the sharp cutting surface of the slicer to cut objects and materials into pieces according to the proportion or width of a point. The slicer is divided into internal slicer and external slicer. Generally, NdFeB material uses internal slicer, and the processed products are mostly thin slices with a general thickness of 0.5-10mm.
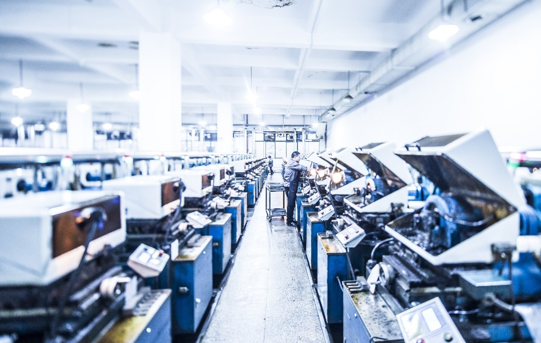
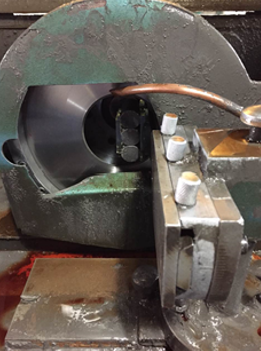
Wire cut Electrical Discharge Machining is a kind of Electrical Discharge Machining (EDM). Wire EDM is to use the electro-corrosion effect generated by pulse spark discharge between two electrodes composed of a metal wire (molybdenum wire, tungsten-molybdenum wire) and the workpiece to process the workpiece to achieve the purpose of forming. The basic principle is the workpiece to be processed is used as the anode, and the molybdenum wire is used as the cathode. The pulse power supply sends out a series of pulse voltages, which are applied to the workpiece and the molybdenum wire. There is enough insulating working fluid between the molybdenum wire and the workpiece. When the distance between the molybdenum wire and the workpiece is small to a certain extent, under the action of the pulse voltage, the working fluid is ionized and broken down, forming an instantaneous discharge channel between the molybdenum wire and the workpiece, generating instantaneous high temperature and causing the metal to melt locally Even vaporized and eroded down. If the work table drives the workpiece to continuously feed, the desired shape can be cut.
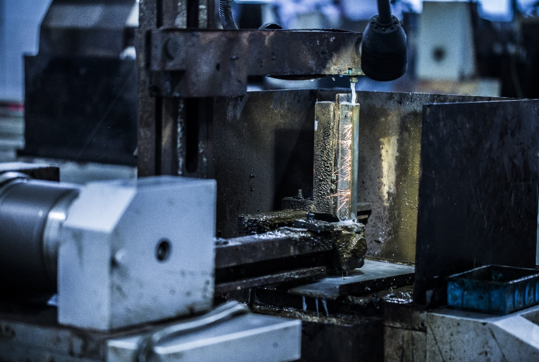
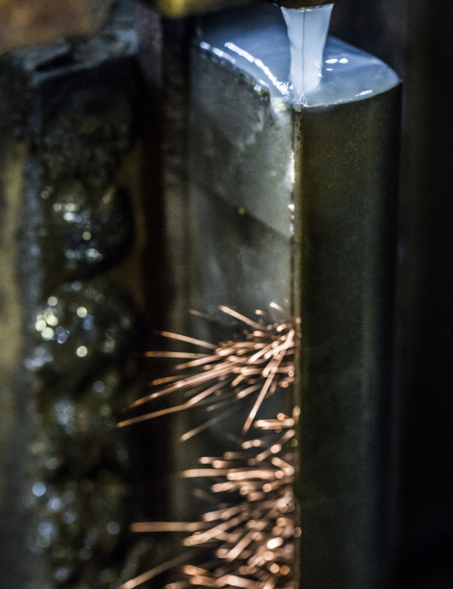
The multi-wire cutting machine is a new type of cutting equipment with a new concept that takes the abrasive into the processed material through the high-speed reciprocating movement of the metal wire, and cuts the processed material into hundreds of slices at the same time. The biggest feature of the multi-wire cutting machine is high production efficiency, high sheet yield, low material loss, and high processing accuracy.
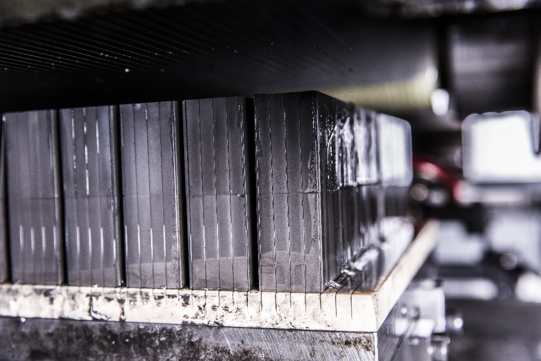

The machining center is developed from a CNC milling machine. The key difference between a CNC milling machine and a machining center is that a machining center is able to automatically exchange machining tools. By installing different kinds of the tools on knife pool, automatic tool change on the spindle of the machining tool can change knives on the clamping device, so that a variety of processing functions can be achieved.
The CNC machining center is a high-efficiency automated machine tool that is composed of mechanical equipment and a CNC system and is suitable for processing complex parts. CNC machining center is currently one of the most widely used CNC machine tools in the world. Its comprehensive processing ability is relatively strong. It can complete more processing content after the workpiece is clamped at one time. Also, its processing accuracy is high. For batch workpieces with medium processing difficulty, its efficiency is 5-10 times that of ordinary equipment, especially it can complete many processes that cannot be completed by ordinary equipment. Additionally, it is more suitable for single-piece processing with more complex shapes and high precision requirements or for small and medium batches of multiple varieties. It concentrates the functions of milling, boring, drilling, tapping and cutting threads on one device, so that it has a variety of technological means.
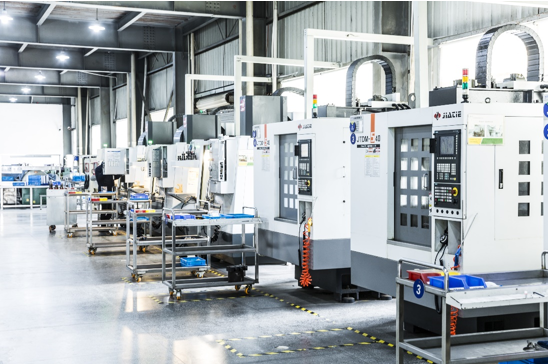
