What is Reliability Testing?
- Share
- Issue Time
- Sep 30,2020
Summary
What is Reliability Testing?
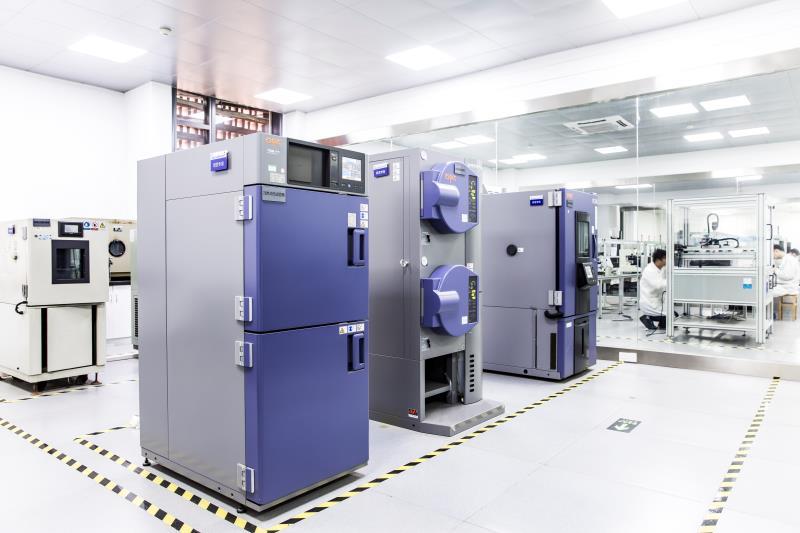
Introduction
Reliability testing is the activity performed to evaluate the maintenance of functional reliability of a product, during a specified lifetime, in all circumstances, such as its intended use, transportation, or storage. Reliability testing is to expose the product to natural or artificial environmental conditions under its effects, in order to evaluate the performance of the product under the environmental conditions of actual use, transportation and storage, and to analyze and study the impact degree of environmental factors and their action mechanism. Through the use of a variety of environmental testing equipment model climate environment of high temperature, low temperature, high humidity and temperature changes, etc., to accelerate the reaction products in the use of the environment condition, to verify whether its reach in the research and development, design, manufacture of the expected quality objectives, to evaluate the product as a whole and, in order to determine product reliability life.
Magnets also undergo a series of reliability tests, such as salt spray test, aging test and pull testing.
Magnet Salt Spray Test (SST)
The salt spray test, a standardized and popular corrosion test method, is applied to inspect corrosion resistance of materials and surface coatings. Usually, the test materials are metallic and finished with a surface coating which can provide a degree of corrosion protection to the underlying metal. With the help of salt spray tester, it is accelerated corrosion test that produces a corrosive attack to coated samples in order to predict the suitability of the coating in use. The test result is evaluated by the appearance of corrosion products (oxides) after a period of time.

Taking Neodymium magnet as an example. Neodymium magnet contains oxides such as Nd and Fe which is easy to get rusty. And oxidation will damage magnet body and reduce magnetic force day by day. Therefore, coating is an essential part of neodymium magnet. Many layers can be used covered NiCuNi, Zn, silver, gold epoxy, phosphating and passivation etc. Different coatings lead to different antioxidant effect. Even with the same coating, types and quality of electroplating process also affect the results. For neodymium magnet which operates in the rain and other harsh environments, the requirement for coating is stricter. Salt spray test is the common method applied to inspect magnet coating.
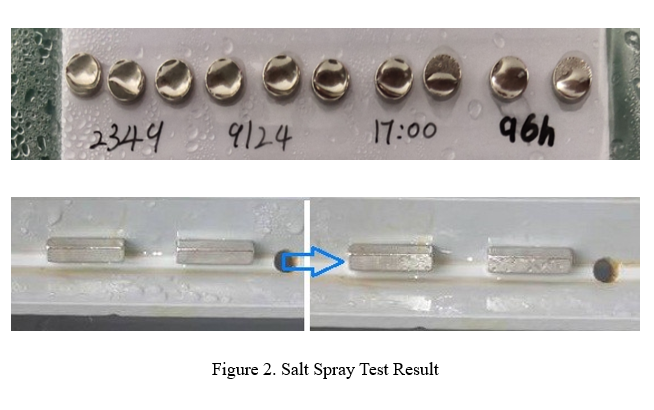
Temperature Resistance Test
Everyone knows that magnetic materials generally have the characteristic of losing their magnetism above the critical high temperature. As the temperature rises, the thermal motion of atoms intensifies, which will disturb the parallel arrangement of the atomic magnetic moments, and the atomic magnetic moments gradually change to Non-parallel arrangement, the magnetism gradually decreases.
Some equipment will generate a certain high temperature when it is running. The magnetic properties of the magnets assembled in the equipment will slowly decay as the temperature rises. For example, as the motor runs at high speed, the temperature of the entire motor will rise,there will be some demagnetization.
Usually in the design stage, we often need to consider the working environment of the magnet and select the appropriate coercive to satisfy the normal operation of the magnet at the corresponding high operating temperature. According to the working environment temperature of the magnet and the magnet assembly condition, we define the temperature of the high temperature demagnetization test and the open circuit and closed circuit conditions.
NdFeB magnets for motors and couplings are tested by VECTOR in the following manner:
1. Measure the flux in open circuit (Helmholtz coil) at room temperature.
2. Place the magnets as in working conditions on an Iron support.
3. Insert the magnets with iron in then oven for 2 hours.
4. When back at room temperature measure again the flux.
5. Calculate the permanent losses (%).

HAST refers to the HAST aging test box. HAST aging test box is widely used for accelerated aging test of IC semiconductors, connectors, circuit boards, magnetic materials, polymer materials, EVA, photovoltaic modules and other related products in the industry.
HAST belongs to unsaturated type, temperature, humidity (70%~100%), pressure can be adjusted according to demand, can do high temperature and high humidity, high and low temperature cycle, double 95, high temperature, high humidity and high pressure test, also known as aging test.
The purpose of accelerated life test is to increase environmental stress (such as temperature) and working stress (voltage and load applied to the product), speed up the test process, and change the life test time of the product or system. The problem of wear and replacement of parts and mechanical parts, what shape the alternating failure distribution function is, and the test to analyze the reasons for the increase in failure rate.
The weight loss test has now become the most direct reference index for evaluating the corrosion resistance and durability of sintered NdFeB permanent magnets.Put the coupled NdFeB nanoparticle sample that has passed accurate mass weighing and size measurement into a high-pressure container. After the sample is tested for a certain period of time under the action of high-temperature and high-pressure water vapor, the surface grains and water vapor produce electrochemical reactions, resulting in The crystal peels off and the surface layer is corroded and powdered; after the test remains, the sample is taken out, the loose corrosive material on the surface is removed, and then weighed. The mass loss (and weight loss) corresponding to the unit magnetic orientation is calculated according to the mass change of the sample before and after the test.
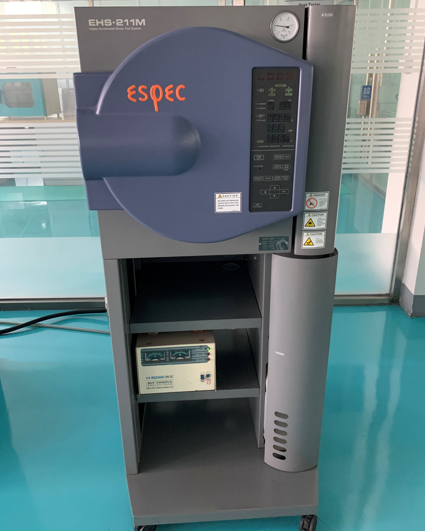
In the weightlessness test, once corrosion pits are formed on the surface of the sintered NdFeB permanent magnet sample, it passes through the expansion of corrosion. After reaching a certain critical point, the sample surface peels off and the corrosion weight loss increases almost linearly with the increase of the test time. The critical point is about 5mg/cm2.
Magnetic materials are widely used in various fields such as wind power generation, new energy vehicles, magnetic levitation trains, intelligent robots, etc. To ensure that the magnet is always effective in the actual application environment, we conduct reliability tests on samples to find out the product’s raw material structure, process, and environment. If there are problems in adaptability, etc., the reliability index of the product can be improved after repeated trials and improvements.
Magnet Pull Testing
It’s common for magnetic assemblies to have a rating of pounds pull (or Max Force) in order to provide users with guidance into the product’s capability. Magnetic pull strength is a reliable method of measuring the maximum strength, or holding power, that a magnetic assembly has before it is separated from a steel plate. It is measured in pounds and obviously, the higher the pull strength, the greater the strength of the magnetic assembly.
Pull tests are the most common method. This requires a pull test scale ( spring loaded scale graduated in ounces or pounds ) and various test fixtures. When comparing test results, whether between different magnet manufacturers or an in-house scheduled audit, it is imperative that the same procedure and apparatus are used in each test. If a smaller ferrous test fixture is used than what was used in the previous test, the results will differ greatly. The reason for this is the larger the ferrous test fixture, more of the magnetic field will be absorbed, therefore, producing higher test results.
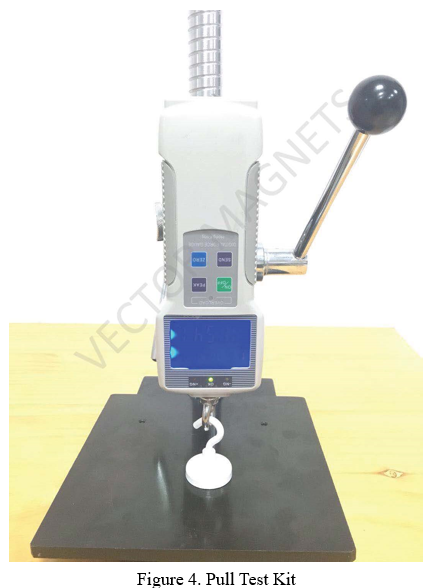
Generally Pull Test Steps
1. Clean and remove any steel objects or dirt from the face of the magnet.
2.Where possible, position the magnet facing up in a horizontal position. attempt o position it such that the force gauge and test piece can be pulled away from the magnet in a perpendicular (right angle) direction.
3.Calibrate the force gauge. Holding the gauge vertically, pull the latch hook down to the reading and allow it to snap back. Adjust the knurled knob so that the maximum reading pointer is set at zero.
4.Select the appropriate test piece and spacer block orientation for the test tobe performed. Attach the test piece to the force gauge and position the spacer block firmly against the magnet face.
Then, firmly holding the test piece, position the test piece on the spacer block.
5.Pull the force gauge slowly and smoothly in a perpendicular (right angle)direction until the test piece breaks away from the magnet.
6.Read the force measurement as indicated by the “maximum reading pointer”. Repeat the test twice and if the same value is achieved, record it in the Magnetic Inspection Log. If the values are different, an additional test should be performed to achieve two agreeing values.
7.A polarity indicating wand has been included in this test kit which has “N” and “S” marked on opposite ends. It can be useful for identifying the north and south pole positions on a magnet and for locating the strongest zone of a particular pole. Since like poles repel and opposites attract, the polarity of a pole can be identified easily.

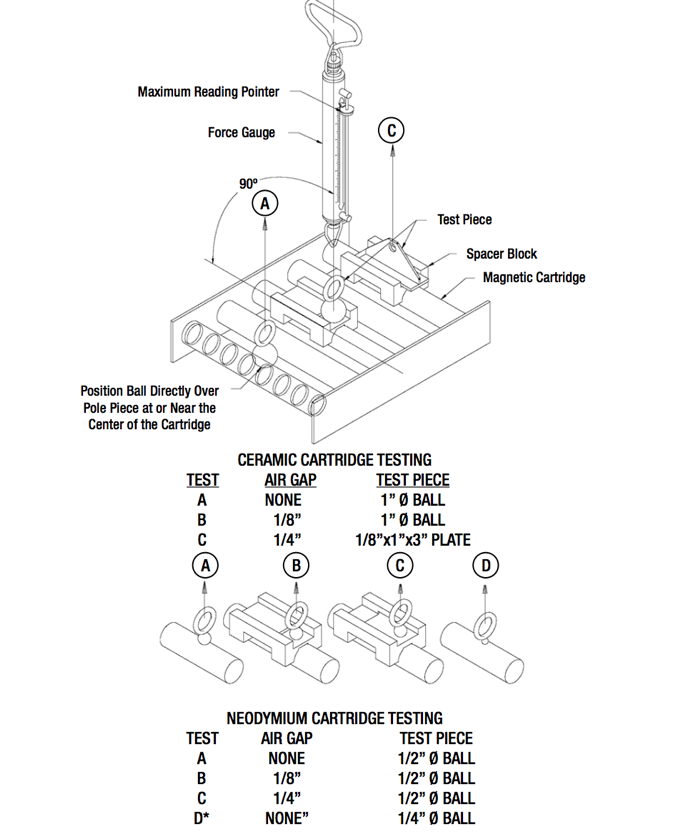