Introduction to the treatment method of stainless steel surface
- Share
- Issue Time
- Jul 24,2020
Summary
The surface of stainless steel is processed by different methods to make the surface of stainless steel have different luster, colors, patterns, etc., to improve the appearance of stainless steel and achieve aesthetic effects.
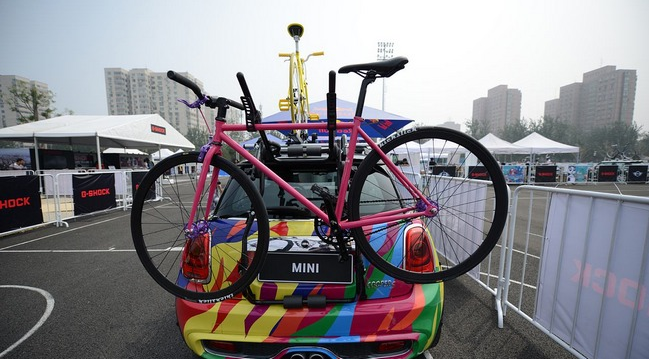
Introduction to the treatment method of stainless steel surface
The surface of stainless steel is processed by different methods to
make the surface of stainless steel have different luster, colors, patterns,
etc., to improve the appearance of stainless steel and achieve aesthetic
effects.
In addition, surface processing has important functions. For example, a
smooth stainless steel surface not only looks clean, but in a corrosive
environment, the smoother the surface, the better the corrosion resistance. In
the processing of stainless steel products (such as deep drawing), the strength
is increased by cold pressing patterns, so that the lines on the metal surface
are slightly rough to catch the grease. A proper amount of grease can reduce
tool wear and reduce tool indentation. The surface processing and coating of
the wire is for the convenience of further processing.
Stainless steel surface processing is usually divided into two
categories. One type is rolling surface processing, the surface obtained by
using different production processes; the other type is deep processing of
stainless steel surface, in order to change the surface level or properties.
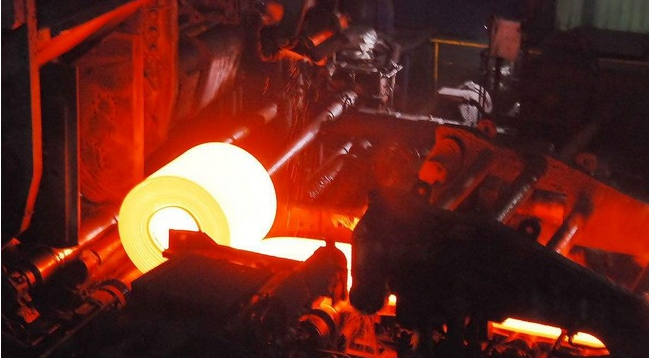
Rolled surface processing
The stainless steel plates and strips produced by rolling mills
generally undergo processes such as hot rolling, cold rolling, annealing,
pickling, and finishing. Because the surface of cold-rolled stainless steel
strip occupies a special position in use, the surface processing of cold-rolled
stainless steel strip is divided into different surface processing types (or
grades) according to different process methods. Stainless steel plate and
strip, especially cold-rolled steel and steel strip, have a variety of surface
processing types. National standards have corresponding regulations, such as
common 2B, No.1, and BA surfaces.
Deep processing of stainless steel surface
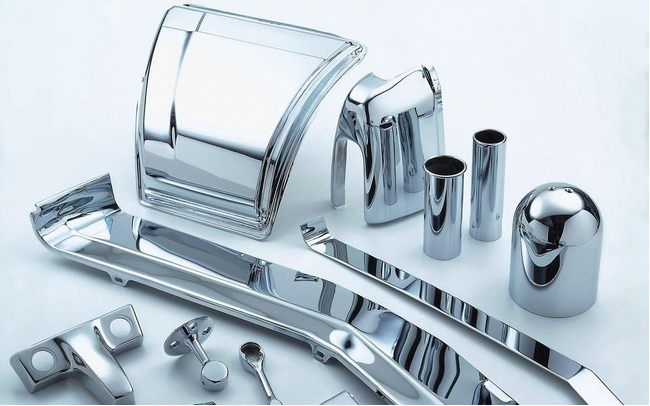
Electroplating and evaporation surface
The surface of stainless steel is covered with a layer of
wear-resistant, scratch-resistant, and corrosion-resistant coating by
electroplating to improve the surface properties of stainless steel. In order
to make the covering layer and the metal matrix firmly bond, different methods
can be used to pretreat the surface to remove the oil and rust on the surface.
The advantage of electroplating is that it has almost no effect on the
microstructure of the base material. The common surface chromium plating and
nickel plating treatments are mainly used for artwork and decoration.
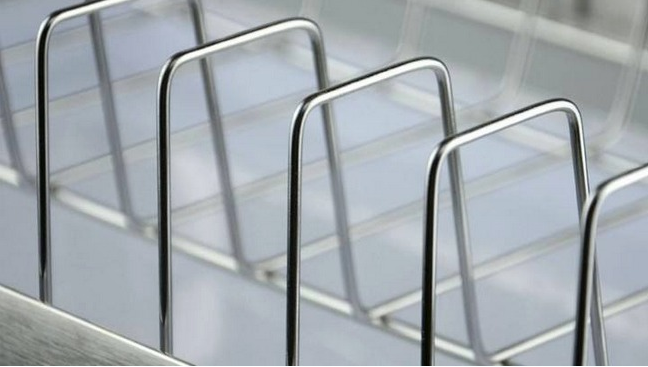
Electropolished surface
The principle of electrolytic polishing is opposite to that of
electroplating. Instead of depositing chromium or nickel on the substrate, it
uses stainless steel as the anode and uses a specially formulated electrolyte
to etch away a thin layer of 2-40PM on the surface of the stainless steel. Make
the metal surface have excellent corrosion resistance and look smooth, clean
and shiny.
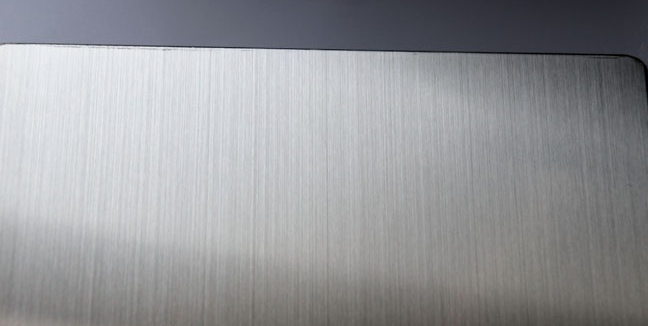
Mechanical polishing is the use of abrasive belts, polishing wheels,
grinding wheels or other tools to grind the surface of stainless steel to
obtain corresponding surface effects. The effects of mechanical polishing
usually include snow wheels, filaments, lotus patterns, matte, and mirror
surfaces.
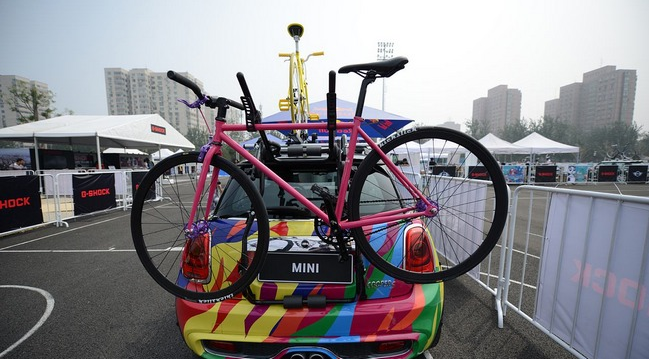
Paint on the surface of stainless steel is a way to protect stainless
steel from oxidation and corrosion. The corrosion phenomenon that occurs around
us refers to the damage of various materials under the action of the
environment (the combined effect of chemical, electrochemical and several
physical factors), performance degradation or state deterioration. However,
spraying paint on the surface of stainless steel is a very important
anti-corrosion maintenance method. A good spray paint protection layer remains
continuous and undamaged, and the combination is good, which can become a
barrier to inhibit the invasion of corrosive media.