High Strength Permanent Magnets: An Untapped Source of Critical Rare Earth Metals but can the Metals be Economically Recovered?
- Share
- From
- http://investorintel.com/
- publisher
- W.Z.
- Issue Time
- Oct 10,2016
Summary
High Strength Permanent Magnets: An Untapped Source of Critical Rare Earth Metals but can the Metals be Economically Recovered?
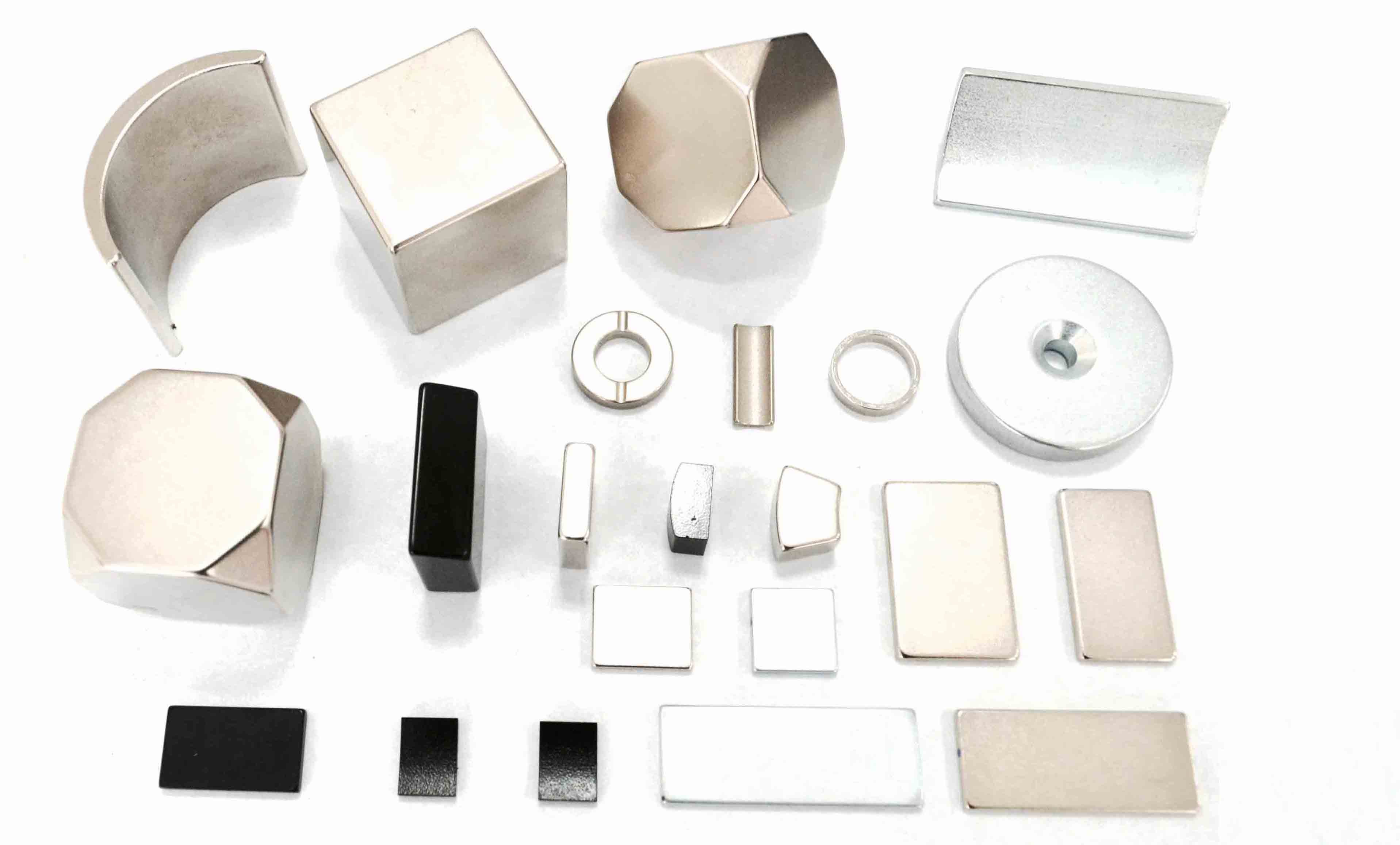
Introduction. Magnet usage is widespread and increasing rapidly as the global economy grows. Most moving vehicles, computers, appliances, high tech devices, head phones, and countless other products contain small motors that use high strength permanent magnets. These remarkable tiny units are employed in a wide range of domestic, commercial, and military equipment. One could say that they are indispensable because ‘they make things work.’ The strongest permanent magnets commercially available are those made from alloys of Nd, Fe, and B (NdFeB) with Sa and Co (SmCo) a close second. Other rare earth elements (REE), such as Dy and Pr may also be present in these magnets. NdFeB magnets are the strongest performers up to 150°C. Between 130°C and 160°C, performance of NdFeB and SmCo magnets overlap. Above 150 degrees °C, SmCo magnets provide greater performance [1]. A variety of magnet grades and configurations is available for specific applications. Because of the high cost of Dy, Nd, and Sm used in magnets and the problems often encountered in getting a reliable supply of these metals, efforts are underway to find rare-earth alternatives [2]. None of these attempts has reached commercial scale indicating that commerce will depend on REE-based magnets for the foreseeable future.
Strong permanent magnets ensure that a wide variety of technologies necessary in our society operate as fault-free and efficiently as possible. The chemical microstructure and chemical composition of these magnets provide macroscopic properties that are unique and valuable for specific product applications. The range of applications using them is amazing and new uses that constantly arise testify to their remarkable value to society. For example, modern vehicles of all types have become “computers on wheels” and contain a large number of micro motors with a wide variety of functions that require miniature, high strength magnets. Locations of these REE magnets in a modern automobile are shown in a Sin-Etsu description [3]. Abraham [4] estimates that a standard vehicle has more than 40 magnets and 20 sensors that use REE. Each hybrid vehicle uses about 1.25 kilograms of REE magnetic material and electric vehicles use about three times more. Mueller, et al. [5] indicate that the first series of electrical cars with NdFeB magnets were introduced to the mass market in 2010. The breakthrough of one million electrical cars produced is estimated by them to be in 2017 with future increases in number exceeding 700%.
Abraham [4] has calculated that wind turbines use as much as two tons of REE magnets each. A large part of this usage is Nd. Approximately 160 kilograms of Dy is included in this amount. Global use of wind turbines is expanding at a rapid rate. Audio and hard disks have become an essential part of private as well as business life worldwide. Permanent high strength magnets make their operation possible. It was estimated in 2013 that the global permanent magnet market had reached $15.1 billion and that this market would grow at a compound annual growth rate of 8.7% and reach $22.9 billion by 2018 [6]. In volume terms, world magnet sales during this period is expected to expand 4.6 percent per year to 1.2 million metric tons. Mueller, et al. [5] point out that demand for NdFeB permanent magnets is expected to increase at an annual rate of 12.5% through 2035.
Magnets retrieved from spent products containing them present a largely untapped above ground (urban) source of these critical REE and other valuable elements associated with them such as Co and B. Accessing this source would provide a valuable contribution to the global supply of REE and would reduce the need to mine them which is fraught with serious environmental problems [7]. Recycling of these metals would also ensure a reliable, domestic source that would reduce present dependence on China for their supply. China currently produces more than 90% of all REE, separates nearly all REE produced globally into individual elements, and produces an increasing fraction of the global supply of rare earth permanent magnets and lamp phosphors [8]. This dependence has serious geopolitical ramifications, especially for the military and defense sectors, since China could withhold this supply at their option, as they did in the case of Japan in 2010 [4]. As will be discussed shortly, recycling these metals from magnets presents challenges. The overall global recycling rate for REE is <1%. Binnemans, et al. [8] attribute the low REE recycling rate to three factors, i.e., inefficient collection, technological difficulties, and a lack of incentives. REE recycling rates are much higher in the few cases where magnets are efficiently collected and processed using REE separation facilities near the site of collection.
Composition of Rare Earth Magnets. According to the International Electrotechnical Commission (IEC) [9], rare earth magnet materials fall into three groups. The magnet material in each of these groups is composed of alloys consisting of REE and certain transition metals. Manufacturing methods, magnet specifications, and mechanical characteristics are available [9]. The three groups are as follows.
- Rare earth-cobalt alloys. The REE is usually samarium, but can also be other light rare earths, i.e., Pr, Ce, Nd or misch metal (combination of Pr and Nd). In some cases, heavy REE such as Gd, Dy, or Er can substitute for the light REE. A ratio of one REE atom to five Co atoms is typically found in these alloys. REE may be 34-39 weight percent of the alloy.
- Rare earth-transition element alloys. Any of the REE listed in (1) can be used to make these alloys. The transition metal content is a Co-rich combination of Co, Fe, and Cu. Small amounts of Zr, Hf, or other metals may also be present to enhance certain desired magnet properties. A ratio of two REE atoms to 13-17 transition metal atoms is usually found in the alloy. The REE content is typically about 23-28 weight percent of the alloy.
- Rare earth-iron alloys. The most common REE in these alloys is Nd, but other REE can be substituted to improve magnet performance. For example, partial substitution of Nd by Dy achieves the higher coercivity required for certain applications such as traction motors of hybrid and electric vehicles [10]. Boron is used in these magnets to control the spacing between Fe atoms [4]. The composition of these alloys is two REE to 14 Fe atoms and one B atom. The REE content of these magnet alloys is 30-35%.
The majority of companies involved in the manufacture and distribution of permanent magnets and in the fabrication of magnetic assemblies and systems for commercial and industrial applications are located in China [11]. Over 70% of the global production of NdFeB magnets (by tonnage) is done in China. China is rapidly changing from a global supplier of REE to a global supplier of products that contain REE [4,8]. This means that China is moving up the value-added chain with the result that products made in China are becoming increasingly common worldwide. At the same time, manufacturing is becoming a lost art in the U.S., a situation that should concern all of us. President Franklin D. Roosevelt commented on the importance of a solid manufacturing base in 1940 [12], just prior to the entry of the U.S. into World War II: Guns, planes, ships, and many other things have to be built in the factories and the arsenals of America. They have to be produced by workers and managers and engineers with the aid of machines which in turn have to be built by hundreds of thousands of workers throughout the land. In 2016, few high-tech magnets, crucial to military hardware, are made in the U.S. and an increasing number of products containing these magnets are made in China [4,13].
REE constitute a significant part of each of the permanent magnet alloy types, with one metal such as Sm or Nd present in high concentration and other metals such as Dy, Pr, Er, and Tm present in much smaller concentrations (<10% by weight) [9,14]. Ability to separate and recover a variety of REE is desirable in order to prevent loss of these valuable resources and to recover value. Other valuable metals such as Co, Cu, B, and Zr are also present. The ability to separate and recover these metals for value would be an added bonus.
Recycling Opportunities. As indicated earlier, our global REE supply comes largely from China. A significant portion of the REE mined in China is mined illegally despite government efforts to control this activity. This illegal activity leads to some uncertainty concerning the quantity of REE mined in China. Mining operations of REE in China are noted for their extensive negative externality effects. Severe environmental damage is present as well as human and animal health problems. The large costs of these ecological problems are absorbed by society, usually at great human health and economic cost [7]. A significant source of the waste generated is a result of the low selectivity of the solvent extraction (SX), ion exchange (IX), and precipitation methods used to separate individual REE. These methods require many stages to achieve desired purities of individual REE because of the very similar chemistry of the REE [14]. Large quantities of solvents and hazardous chemicals are used with little environmental control of their disposition. These separation methods have been described in detail [14].
Benefits to society of recycling metals have been summarized [8,15]. National security that comes from a secure and reliable domestic source of REE heads the list. China used its monopoly on REE production and supply as an economic weapon against Japan during the 2010 conflict over ownership of islands in the sea bordering the two nations [4]. This cut-back in supply was of great concern because REE are essential to the production of high-technology products produced and marketed in Japan. A fallout from this experience was greater effort expended by Japan to develop recycling capacity, including recycling of REE from spent magnets. There has been political unrest in several nations in central Africa for decades [4]. Yet, some of these countries are rich in metal resources such as Co needed for production of CoSm magnets. Recycling of Co from spent magnets could partially alleviate this concern.
The six top rare earth mine producing countries in 2015 were China (105,000 tons), Australia (10,000 tons), United States (4,100 tons), Russia (2,500 tons), Thailand (1,100 tons), and Malaysia (200 tons) [16]. MolyCorp, the only producing REE mine in the U.S., ceased operation and filed for bankruptcy in 2015 leaving the U.S. with zero production [16]. It is obvious that a significant recycling effort is required to make an appreciable contribution to the yearly output of REE. Binnemans et al. [8] observe that a drastic improvement in the recycling of REE is an absolute necessity. These authors point out that recycling eliminates the major problem of having to mine REE ore containing all REE in order to obtain one or more single REE. For example, recovering Nd and Dy from spent FeNdB magnets eliminates the need to discard or otherwise dispose of other surplus REE that would be present in mined ore. In addition, recycling these metals reduces the amount of virgin ore that needs to be mined and processed, conserves a valuable resource, and avoids the extreme environmental and health effects that accompany REE mining.
REE usage is projected to increase substantially in the future due to increasing demand for magnets and products containing them by a rapidly expanding, affluent global society. Thus, it is prudent to develop reliable, secondary sources for these metals. An inevitable consequence of mining is that ore grades decrease necessitating the need to find new deposits or go to greater depths of existing deposits. Effective recycling can partially alleviate these effects extending the lifetime of existing REE deposits.
Mining has high energy and water requirements [17]. Recovery of metals through recycling results in significant reduction in the amount of mining required with associated reduction in coal combustion, carbon dioxide emissions, land and water use, and impacts on the biosphere. A further important benefit of recycling is the reduction in the discard of solid, liquid, and/or gaseous waste into surrounding land, streams, and atmosphere which is common in many processes, where environmental regulations either do not exist or are poorly enforced, as is the case with REE in China [7].
Recycling insures that fewer toxic metals inherent in mining activities as “unwanted companions” enter the technosphere. Thorium and U and their decomposition products are commonly found in REE deposits. Unless great care is taken, these toxic metals enter the environment through discard to tailings, emissions to the atmosphere, and inefficient beneficiation processes. The effect of these toxic metals on the environment and on human health have been documented [17].
Recycling can partially decouple production of technology metals from major metal sources from which they are derived as by-products. The main objective of producers of commercial metals is production of major metals, not of by-product metals. Production of technology metals is nearly always tied to the production of a major metal. For example, the Baiyun Obo REE mine in China is the largest REE mine in the world [14], but it is, primarily, an Fe mine with REE being a by-product. Any success in decoupling this link through recycling is advantageous to the security of the technology metal supply.
Effective recycling of REE makes possible dampening of price fluctuations by improving the supply-demand balance and limits speculation by broadening the supply base [18]. The REE market would benefit greatly by a reliable supply of recycled metals. The REE market from mining to production and sale of > 99% pure products is dominated by China. Prices for individual REE have fluctuated widely during the past decade. The critical rare earth metals, Nd, Y, Eu, Dy, and Tb, are essential for the function of high technology products, yet, individually, they are worth very little. The incentive for recycling them is not high [8] even though this source is desirable to broaden the supply base and increase national security.
This situation has attracted the attention of several groups who are developing recycling processes for recovery of Nd and other critical REE from high performance magnets. Dupont and Binnemanns [19] are among the leaders in this effort as is the Critical Materials Institute in the U.S.A novel separation procedure using ionic liquid extractants has been developed by Dupont and Binnemanns [19]. Ionic liquids have significant advantages over organic solvents including non-volatility and non-flammability. Using this method, the valuable elements, Dy, Nd, and Co, were readily separated from magnets in high purity. In a separate effort, discussed below, the Ucore/IBC group is well on the way to the production of Dy and other rare earth metals from pregnant leach solutions derived from U.S. ore deposits at pilot plant scale using a Molecular Recognition Technology (MRT) process [18,20-23]. The MRT procedure can be used to recycle individual REE. Hopefully, recycling efforts underway will bring some stability to the critical rare earth market by improving the supply-demand balance for these important metals.
Recycling Technologies. Excellent reviews of technologies used for separation and recovery of REE, individually or as groups, are available [5,8,14,18,24,25]. Goode [25] has described technologies used and being developed for the separation of REE. His conclusion is that SX is the predominant technology used in the processing of mined REE ore. He indicates that MRT is a promising technology based on its performance in separation and recovery of REE. In general, technologies based on SX or variations of it are those used in efforts to develop recycling processes for recovery of metals of value from spent high performance magnets and other secondary sources. Besides spent permanent magnets, these sources include lamp phosphors; ashes, such as coal ash; mine tailings, often rich in REE waste; and phosphorites.
In Table 1, steps necessary to achieve effective recycling of REE from high performance spent magnets at commercial scale are given. Although the global recycling of REE is < 1%.
__________________________________________________________________
Table 1: Steps required for effective recycling of rare earth elements from high performance spent magnets
__________________________________________________________________
- have available for recycling an adequate and continuing supply of magnets
- have capability to treat magnets on large scale to obtain REE in a form such as a leach solution from which the REE can be separated and recovered
- have technology available that is capable at laboratory scale of making separation and recovery of REE from a test (leach) solution at desired purities (>99%)
- achieve scale up of the technology in item 3 to pilot plant scale with separation and recovery capabilities at >99%
- establish that laboratory scale separations and recovery can be reproduced at pilot plant scale to produce REE at kilogram levels at >99%
- have pilot plants scaled up to commercial plants capable of multi ton competitive REE separation and recovery
__________________________________________________________________
The rate is much higher where collection and processing are available at the same location (Table 1, items 1 and 2). Solvay in a cooperative venture with Umicore has developed a commercial process based on SX for separation and recovery of selected REE from spent magnets [26]. Technologies developed by Solvay for REE recycling are similar to those used in mining processes adapted to specific characteristics present in urban mines. The intent of Solvay in opening this recycling unit is to diversify its sources of supply and preserve resources. Lifton [27] gives insight into the recycling complexities faced by companies in Japan as they attempt to recover REE from spent magnets. Companies in Japan and western Europe are global leaders in the effort to develop commercial REE recycling operations.
Izatt and Hagelüken [15] have presented and discussed reasons that REE are usually not recovered from spent magnets. First, these magnets are small and, generally, are used in products that are dispersed widely providing little incentive to collect them for recovery of the REE they contain. Second, when used in single products such as automobiles the special effort needed by an owner to recover the magnets at the time of disposal is unlikely. Third, products such as wind turbines that each contain large quantities of REE have a lifetime of decades and few spent turbines are yet available for magnet recovery. In the future, spent turbines and other long life-time products may be an excellent source of REE.
Scaling laboratory results to pilot plant level presents many challenges (Table 1). It is necessary that this scaling be accomplished in order to increase the recycling rates of these important metals. It would be especially desirable to have relatively small modular commercial plants that could be used globally at local sites where products containing magnets might be collected. Expenses and time required to transport such collected products to recycling operations such as Solvay is prohibitive, but a modular separation system on site could be economically sustainable. Having achieved items 1-5 (Table 1), MRT presents such a possibility.
Molecular Recognition Technology. MRT has been proven at both the lab and pilot scales as a green chemistry process for separation and recovery of REE from ore-derived pregnant leach solution (PLS). Based on this successful work, MRT holds great promise for separation of individual REE from secondary sources, such as magnets following their dissolution in an appropriate acid. The MRT process has been described [18,20,28]. Individual separations of the entire suite of sixteen REE, at > 99% purities, from a PLS derived from the Bokan-Dotson Ridge deposit at lab-scale, with subsequent separation of 99.99% pure Dy, as well as separation of > 99% pure strategic REE sub-groups, at pilot scale have been accomplished. Purity of the 99.99% Dy was confirmed by two independent laboratories. Greater than 99% of the REE were recovered from the PLS at both lab and pilot scales [18,21-23,28,29].
Based on successful laboratory and pilot scale work, the MRT REE separation system has demonstrated several advantages over conventional processes for REE separations. First, the MRT system is based on green chemistry principles throughout. Minimal waste is generated. No solvents are used. Few chemicals are used and those used in washing and elution of columns are as benign as possible. Energy requirements are minimal with separations performed at room T (~25°C) and P (~0.1 MPa). Second, high selectivity of the SuperLig® products makes possible separation and recovery of REE from the PLS at >99% levels and subsequent separation of individual REE at >99% levels. Results of these high recovery levels are achievement of maximum economic value, minimal loss of REE to tailings or other sectors, many fewer stages required to achieve given REE purities compared to conventional separation systems, and reduced use of auxiliary substances. Third, the entire MRT operation is physically and operationally simple, reducing space as well as capital and other costs. Fourth, the MRT operation requires fewer personnel, equipment, and chemicals, thereby reducing operating costs. Fifth, the green chemistry MRT operation should readily meet stringent environmental standards in the U.S. Sixth, Dy or other individual REE can be separated in a targeted manner from the REE groups or subgroups without the need to first separate low‐value rare earths such as Ce and La. This greatly reduces metal inventories and working capital costs.
Operating expense and capital expense costs for MRT compared to SX for separation and recovery of REE have been estimated [18]. Relative costs for the two technologies can be summarized as follows: capital expenses (floor space and equipment cost) are small for MRT, large for SX; operating expenses (processing costs, labor, safety provisions, spent chemical and waste water discard, REE processing time, REE inventory time) are small for MRT, large for SX. Costs associated with solvent use and recovery/disposal are non-existent for MRT and high for SX. Recovery rates for REE are high for MRT and much lower for SX depending on the care taken with the SX system. MRT systems are much simpler in design than SX systems. Reaction kinetics are fast for MRT systems, but slow for SX systems.
Lifton [27] has pointed out that the economics of recycling are simple. Production of metals from mined ore is logistically, water, and energy intensive. Capital and operating costs of these operations are gigantic. Thus, whenever there is a supply chain of scrap and/or spent REE-containing products, such as magnets, that can be cheaply processed for recovery of target metals without the cost of the original production energy and logistics of the mined ore, the recovered metals will be eagerly purchased by operators of that supply chain so long as the cost is less than “new” material. This assessment is in line with the arguments in this article and MRT is uniquely situated to capitalize on the recycling opportunity.
High selectivity of the MRT process and the use of benign chemicals result in markedly lowered capex and opex costs. The number of stages required to reach a desired purity level is much lower for MRT than SX because of the higher selectivity of MRT processes. The result, as indicated above, is reduced space requirements as well as lower equipment, processing, labor and waste treatment costs. High REE recovery rates coupled with rapid processing times maximize the financial rate of return and minimize working capital needs due to low metal inventories. MRT is a green chemistry process of the type needed in 21st century REE separations either from PLS derived from ore or solutions derived from secondary sources such as magnets. Increasingly stringent environmental and health standards for separation technologies must be achieved in accord with intensifying demands for economic efficiency as REE applications continue to expand. The simple design of MRT systems makes it possible to prepare modular units capable of making commercial separations on a regional basis of selected REE from collected spent magnet feedstock.
References
1. Neodymium Magnets: An Expert Information Source, Accessed September 9, 2016.
2. Tecschlet, L. The Coming Revolution in High-strength Magnets, Design World, December 18, 2014. Accessed September 12, 2016.
3. Shin-Etsu Rare Earth Magnet, Accessed September 12, 2016
4. Abraham, D.S. 2015. The Elements of Power: Gadgets, Guns, and the Struggle for a Sustainable Future in the Rare Metal Age. Yale University Press, New Haven, Connecticut.
5. Mueller, S.R., Wäger, P.A., Widmer, R., Williams, I.D. 2015, A Geological Reconnaissance of Electrical and Electronic Waste as a Source for Rare Earth Metals, Waste Management, 45, 226-234.
6. BCC Research, Accessed September 12, 2016.
7. Yang. X.J., Lin, A., Li, X.‐L., Wu, Y., Zhou, W., Chen, C.Q. (2013), China’s Ion‐adsorption Rare Earth Resources, Mining Consequences and Preservation, Environmental Development, 8, 131–136.
8. Binnemans, K., Jones, PT., Blanpain, B., Van Gerven, T., Yang, Y., Walton, A., Buchert, M. 2013. Recycling of Rare Earths: A Critical Review, Journal of Cleaner Production, 51, 1-22. Accessed September 10, 2016.
9. IEC Standard Publication 404-5 “Methods of Measurement of Magnetic Properties of Magnetically Hard (Permanent Magnet) Materials or the “MMPA Permanent Magnet Guidelines” MMPA Standard No. 0100-00. Accessed September 14, 2016.
10. Van Ende, M-A., Jung, I-H., Kim, Y-H., Kim, T-S. 2015. Thermodynamic Optimization of the Dy-Nd-Fe-B System and Application in the Recovery and Recycling of Rare Earth Metals from NdFeB Magnets, Green Chemistry, 17, 2245-2262.
11. Benecki, W.T., Clagett, T.K., Trout, S.R., 2010. Permanent Magnets 2010-2020: A Comprehensive Overview of the Global Permanent Magnet Industry, Accessed September 12, 2016.
12. American-Made National Security: America’s growing and dangerous reliance on foreign nations for the products needed to defend the American people puts us at serious risk, Alliance for American Manufacturing, Accessed September 12, 2016.
13. Izatt, R,M., Military Success, Rare Metals and the Periodic Table, 2016. Accessed September 14, 2016.
14. Zhang, J., Zhao, B., Schreiner, B. 2016. Separation Hydrometallurgy of Rare Earth Elements, Springer, New York.
15. Izatt, R.M., Hagelüken, C. 2016. Recycling and Sustainable Utilization of Precious and Specialty Metals, In Izatt, R.M. (Ed.), Metal Sustainability: Global Challenges, Consequences, and Prospects, Wiley, Oxford, U.K.
16. 6 Top Rare Earth-production Countries: A Look at Rare Earth Production, Accessed September 12, 2016.
17. Izatt, R.M., Izatt, S.R., Bruening, R.L., Izatt, N.E., Moyer, B.A., 2014, Challenges to Achievement of Metal Sustainability in Our High‐Tech Society, Chemical Society Reviews, 43, 2451–2475.
18. Izatt, S.R., McKenzie, J.S., Bruening, R.L., Izatt, R.M., Izatt, N.E., Krakowiak, K.E., 2016. Selective Recovery of Platinum Group Metals and Rare Earth Metals from Complex Matrices using a Green Chemistry-Molecular Recognition Technology Approach. In Izatt, R.M. (Ed.), Metal Sustainability: Global Challenges, Consequences, and Prospects, Wiley, Oxford, U.K.
19. Dupont, D., Binnemans, K., 2015. Recycling of Rare Earths from NdFeB Magnets using a Combined Leaching/Extraction System Based on the Acidity and Thermomorphism of the Ionic Liquid [Hbet][Tf2N], Green Chemistry, 17, 2150-2163.
20. Izatt, R.M., Izatt, S.R., Izatt, N.E., Krakowiak, K.E., Bruening, R.L., Navarro, L., 2015, Industrial Applications of Molecular Recognition Technology to Green Chemistry Separations of Platinum Group Metals and Selective Removal of Metal Impurities from Process Streams, Green Chemistry, 17, 2236–2245.
21. Press Release: June 7, 2016, Ucore Separates HREE and LREE Classes at 99%+ Purity via SuperLig®-One Pilot Plant, Accessed September 14, 2016.
22. Press Release: July 5, 2016, Ucore Separates Dy and Ho Sub-Groups at 99%+ Purity via SuperLig®-One Pilot Plant, <http://ucore.com/press-releases> Accessed September 14, 2016.
23. Press Release: August 15, 2016, Ucore Produces 99.99% Dysprosium via SuperLig®-One Pilot Plant, <http://ucore.com/press-releases> Accessed September 14, 2016.
24. Gupta, C.K., Krishnamurthy, N. 2005. Extractive Metallurgy of Rare Earths, CRC Press, New York.
25. Goode, J.R. 201X. Options for the Separation of Rare Earth Elements, Accessed September 5, 2016.
26. Press Release, September 27, 2012 Solvay: Accessed September 8, 2016.
27. Lifton, J., Lifton on Rare Earth Recycling the Right Way, Accessed September 14, 2016.
28. Izatt, S.R., McKenzie, J.S., Izatt, N.E., Bruening, R.L., Krakowik, K.E., Izatt, R..M., Molecular Recognition Technology: A Green Chemistry Process for Separation of Individual Rare Earth Metals, Accessed September 14, 2016.
29. Press Release: September 26, 2016, Ucore Confirms Success of SuperLig®-One Pilot Plant via Independent Analysis, Accessed September 26, 2016.