Honda engineers scaled back rare earth metals in hybrid engines significantly
- Share
- From
- TECHNICA
- publisher
- Vector Magnets
- Issue Time
- Jul 22,2016
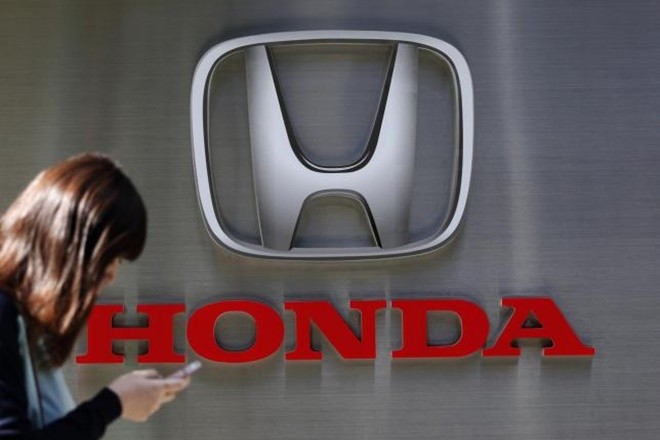
Honda said on Tuesday that it had created the first commercial hybrid-electric vehicle motor without using any heavy rare earth metals. (Rare earth metals are often divided into “heavy” and “light” categories.) Working with the expertise of Daido Steel Co., Honda’s new motor will appear in this year’s Honda Freed, a hybrid minivan sold in Japan.
Rare earth metals are essential to making a plethora of items, including smartphones, laptops, missiles, and electric cars. Unfortunately, that group of elements are at risk of shortage, and many of them are mined predominantly in China, adding a special political flavor to ensuring a global supply for industry. In 2009, Reuters reported that Toyota, maker of the popular hybrid-electric Prius, risked suffering at the hands of a rare earth metal shortage. And in 2010, China temporarily banned exports of rare earth metals to Japan during a standoff over territory.
Honda’s press release adds that a magnet made of rare-earth metal neodymium is necessary for a hybrid motor, but without the addition of heavy rare earth metals like dysprosium or terbium, the neodymium magnet is susceptible to damage and performance issues from exposure to high temperature. Daido Electronics (a subsidiary of Daido Steel) worked with Honda to develop a neodymium magnet that could tolerate high temperatures without help from heavy rare earth metals. Instead of sintering the neodymium magnets (a process that can use heat to compress an element but doesn’t liquify it), Daido used a “hot deformation” process to make the magnets. According to Honda and Daido, the hot deformation technique “enables nanometer-scale crystal grains to be well-aligned in order to realize a fine crystal grain structure that is approximately ten times smaller than that of a sintered magnet, which makes it possible to produce magnets with greater heat resistance properties.”
While this method had been tested before, Honda took the tests a step further by preparing to use hot deformation magnets in a production vehicle. Specifically, it revised the shape of the magnet and the rotor to “to optimize the flow of the magnetic flux of the magnet.”