What's magnetic deviation angle?
- Share
- Issue Time
- Feb 8,2025
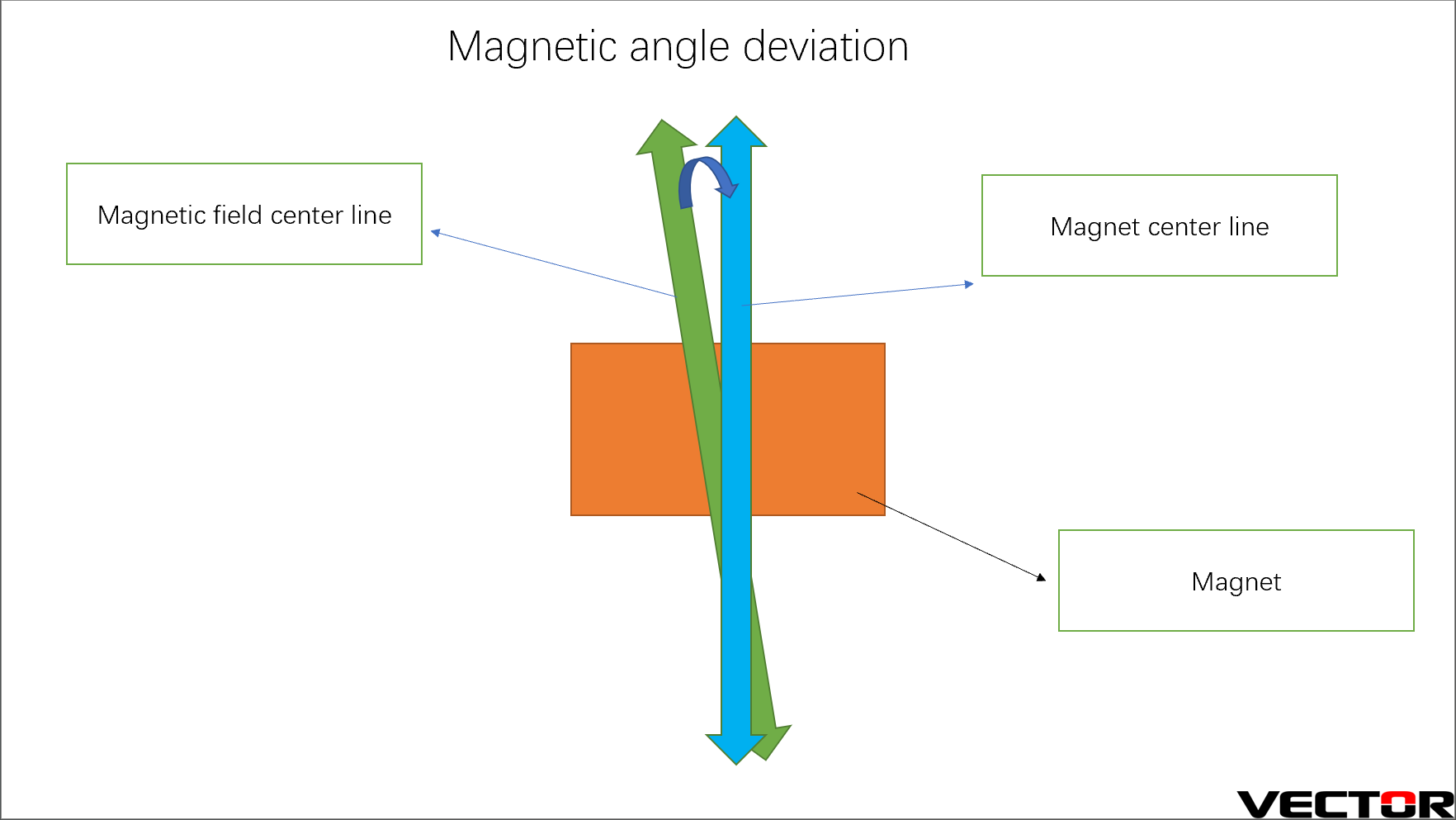
Magnetic Deviation Angle of Permanent Magnets
Definition:
The magnetic deviation angle refers to the angular difference between the actual and the ideal magnetic dipole moments of a magnetized permanent magnet. It measures the deflection of the magnetization vector from its intended direction.
Causes of Magnetic Deviation Angle
1. Uneven Material Composition:
Inconsistent material distribution or crystalline structures within the magnet can result in irregular magnetization, causing a magnetic deviation.
2. Manufacturing Process Issues:
Imperfect application of a magnetic field during magnetization or suboptimal heat treatment processes can lead to a magnetic deviation angle.
3. External Magnetic Field Interference:
Nearby magnetic fields can alter the magnetization direction during the magnet’s manufacturing or application, contributing to magnetic deviation.
4. Temperature Changes:
Thermal fluctuations can affect the arrangement of magnetic domains, leading to deviations in the magnetization direction.
5. Mechanical Stress:
Shocks, mechanical stress, or vibrations may shift the orientations of magnetic domains, resulting in magnetic deviation.
Impact on Motors
1. Reduced Efficiency:
- A large magnetic deviation angle may prevent the magnet’s full utilization, lowering motor efficiency.
- The existence of magnetic deviation increases stray magnetic fields and leads to magnetic flux leakage, reducing the effective utilization of the magnetic field.
2. Speed and Torque Issues:
- Excessive deviation may misalign the rotor and stator magnetic fields, resulting in speed inconsistencies and failure to meet design specifications.
- Torque output can be affected, causing the motor to underperform within its designed torque range.
3. Increased Noise and Vibration:
- Larger magnetic deviation angles exacerbate motor noise and vibration due to the formation of asymmetric magnetic fields.
- These vibrations can impact smooth motor operation and shorten its service life.
4. Cogging Torque Problems:
- Magnetic deviation increases cogging torque, causing torque fluctuations during motor operation.
- Even with design optimizations like segmented skewed poles, severe magnetic deflection can undermine these improvements.
Impact on Sensors
1. Reduced Accuracy:
- Excessive magnetic deviation may lead to misalignment of the sensor with the magnetic field, reducing measurement accuracy.
- For instance, in magnetic angle sensors, large deviations can cause significant angle measurement errors.
2. Limited Sensing Range:
- Magnetic deviation can restrict the sensor’s ability to sense magnetic fields within its designed range.
- In high-precision magnetic angle sensors, deviations beyond ±3° can impair sensor performance.
3. Increased System Error:
- Misalignment between the sensor and the magnetic field due to magnetic deviation increases system nonlinearity errors (INL).
- For example, MPS’s MA600 magnetic angle sensor can reduce INL to 0.1° after user calibration, but excessive magnetic deviation can render calibration ineffective.
Recommendations for Mitigation
1. Material Optimization:
- Use high-quality, homogeneous materials to ensure consistent magnetization.
2. Process Control:
- Optimize magnetic field application during magnetization and maintain stringent heat treatment controls.
3. Environmental Protection:
- Shield magnets from external magnetic fields during manufacturing and application.
4. Temperature Management:
- Maintain stable operating temperatures to reduce domain rearrangement.
5. Mechanical Protection:
- Minimize exposure to mechanical stress, shock, and vibration.
By addressing these factors, manufacturers can reduce the magnetic deviation angle, thereby improving motor performance and sensor accuracy.