What is a magnetic polishing machine and what is the principle of a magnetic polishing machine?
- Share
- Issue Time
- Mar 11,2024
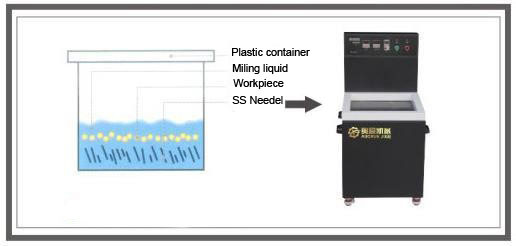
Magnetic polishing machine is also
called magnetic tumbler. This polishing equipment breaks through the
traditional vibration grinding and polishing concept. It uses magnetic force to
drag the stainless steel needle grinding material to produce rapid rotational
motion, thereby achieving multiple effects such as burr removal, polishing, and
cleaning. Utilizing its unique magnetic field distribution to produce a strong
and stable magnetic induction effect, the magnetic steel needle and the
workpiece are fully ground in all directions and at multiple angles to achieve
rapid rust removal, dead corners, burr removal, oxide film and sintering
traces. and other effects. Especially for workpieces with complex shapes,
porous gaps, internal and external threads, etc., it can show its magical
effect. It does not damage the surface of the workpiece and does not affect the
accuracy of the workpiece. Make the workpiece instantly smooth, tidy and brand
new. Suitable for grinding and polishing gold, silver, copper, aluminum, zinc,
magnesium, iron, stainless steel and other metals and non-metallic workpieces
such as hard plastics. After being processed by this type of polishing machine,
the surface of the workpiece will show the original metallic luster, which is
bright and round and has a visual effect; it can also release part of the
internal stress of the workpiece and improve the mechanical properties of the
workpiece; strengthen the surface quality of the workpiece and improve the
surface performance.

Features of magnetic polishing machine
1. Achieve multiple functions such as
deburring, chamfering, polishing, and cleaning;
2. For irregular-shaped parts, dead
corners such as holes and tubes, and cracks can be polished without any dead
corners;
3. The equipment can set the time, the
processing speed is fast, the operation is simple and safe, the end reminder
can remind the polishing to be completed, and one person can operate multiple
machines; the polishing process does not require manual intervention;
4. Variable frequency adjustment to meet
various polishing needs. Stainless steel needles are available in different
diameters from 0.2-5MM to 1.2-10MM;
5. After grinding, the workpiece will
never be deformed, the surface will not be damaged, the accuracy will not be
affected, and the shape and size will not change. The surface roughness value
can reach Ra0.1-Ra0.01, and the surface shows bright metallic luster;
6. Low cost, the grinding time is about
2-20 minutes to complete; the operation is simple, convenient, completely
technology-free, and can be operated by multiple machines;
Application scope of magnetic polishing machine
Suitable for grinding and polishing
gold, silver, copper, aluminum, zinc, magnesium, titanium, stainless steel and
other metals and non-metallic workpieces such as hard plastics.
Such as: 1. Precision stamping parts; 2.
Stainless steel, copper and other metal parts, screw threads; 3. Magnesium
aluminum die-cast parts;
4. Zinc and aluminum die-cast parts; 5.
Precision spring and spring parts; 6. Electronic, computer, and communication
parts;
7. Centering, tooling, CNC automatic
lathe parts; 8. Mobile phone casing, communication metal casing
Disadvantages of magnetic polishing machine:
1. The consumables are the martensite
stainless steel needle and the grinding fluid used;
2. The current and voltage required for
work are relatively large, which can easily cause safety hazards;
3. Power consumption is fast, machine
parts wear out quickly, and maintenance costs are relatively high;