A Comparison of Position Sensors: Resolver, AMR Sensor, Hall-Effect Sensor, IPS, Optical Encoder...
- Share
- Issue Time
- Aug 3,2023

Comparing Position Sensors: An Overview of Resolver, AMR Sensor, Hall-Effect Sensor, IPS, Optical Encoder and Resistive Contacting Sensor
Position sensors play a crucial role in measuring the angle or position of rotating objects, enabling precise control and monitoring in various applications.
In this post, we will explore and compare different types of position sensors, including Resolvers, AMR Sensors, Hall-Effect Sensor, IPS, Optical Encoder, and Resistive Contacting Sensors. Each sensor has its own unique characteristics and advantages, making them suitable for different use cases.
Resolver:
Resolver is a high-precision position sensor that excels in accuracy and robustness, making it suitable for demanding applications. It works based on electromagnetic induction principles and provides accurate measurements even in harsh environments with high levels of electrical noise and interference. However, resolvers are relatively larger in size and more expensive compared to some other sensor types.
AMR Sensor:
AMR (Anisotropic Magneto-Resistive) sensor is known for its high sensitivity and low power consumption. It can detect small changes in magnetic fields, making it suitable for applications requiring precise measurements. AMR sensors are compact, durable, and offer excellent performance in detecting rotational movements. However, they may have limitations in extremely high-speed applications.
Hall-Effect Sensor:
Hall-Effect sensors utilize the Hall-effect phenomenon to measure the position of a rotating object. They offer quick response, high-frequency capability, and are available in both contact and non-contact variants. Hall-Effect sensors are widely used due to their reliability, cost-effectiveness, and versatility. However, they may have limitations in terms of resolution and accuracy compared to some other sensor types.
IPS (Inductive Position Sensor):
IPS is based on the principle of electromagnetic induction. It consists of fixed and rotating coils that detect changes in inductance to determine the position of an object. IPS sensors provide accurate measurements and are resistant to environmental factors such as dust and moisture. However, they may have limited angular range and require calibration for optimal performance.
Optical Encoder:
Optical encoders use optical principles to measure the angle or position of a rotating object. They consist of a rotating optical disc and a stationary photodetector. Optical encoders offer high resolution, and fast response, and are capable of providing precise measurements. However, they can be sensitive to dust, and vibrations, and require careful installation and alignment.
Resistive Contacting Sensor:
Resistive contacting sensors rely on changes in resistance to determine the position of a rotating object. They feature a fixed resistor and a contacting point that moves with the object. Resistive sensors are cost-effective and simple in design. However, they may be prone to wear and tear due to physical contact, leading to potential reliability issues over time.
Conclusion:
Each position sensor type discussed—Resolver, AMR Sensor, Hall-Effect Sensor, IPS, Optical Encoder, and Resistive Contacting Sensor—offers unique advantages and trade-offs. The choice of the sensor depends on specific application requirements, such as accuracy, environmental conditions, cost, and size constraints. Understanding the characteristics of different position sensors helps engineers select the most suitable option to achieve accurate and reliable position measurement in their systems.
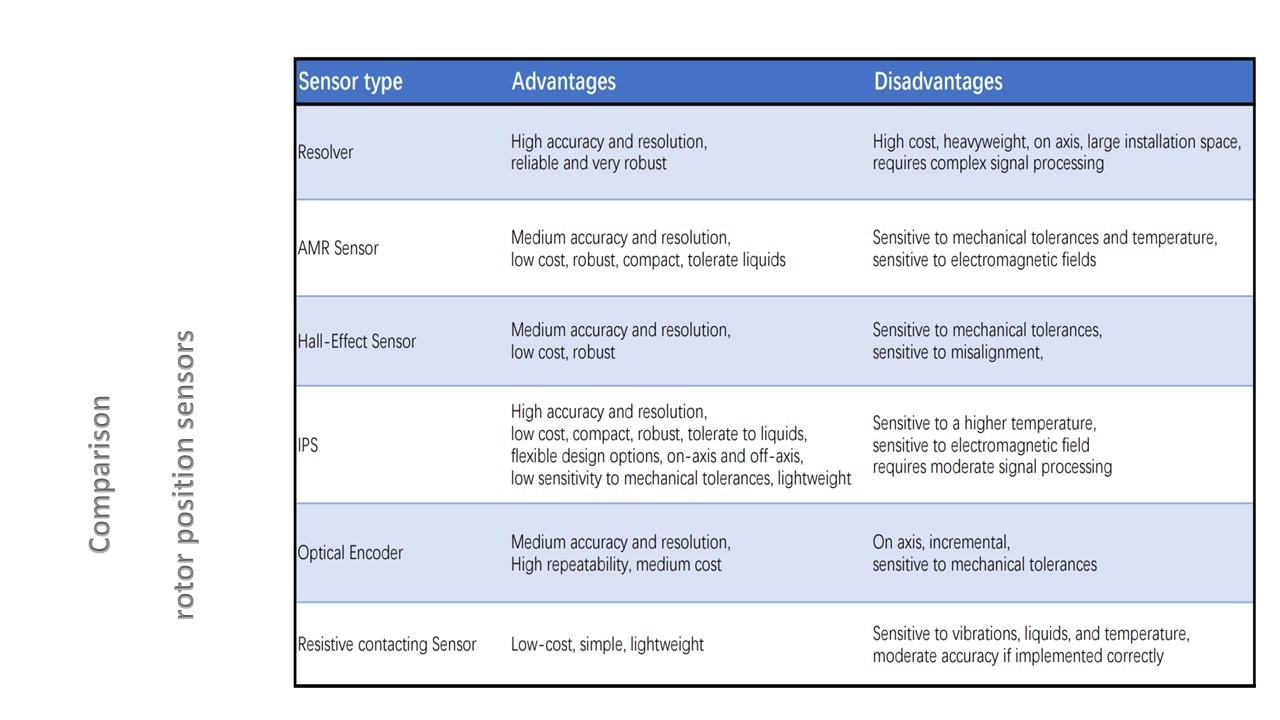